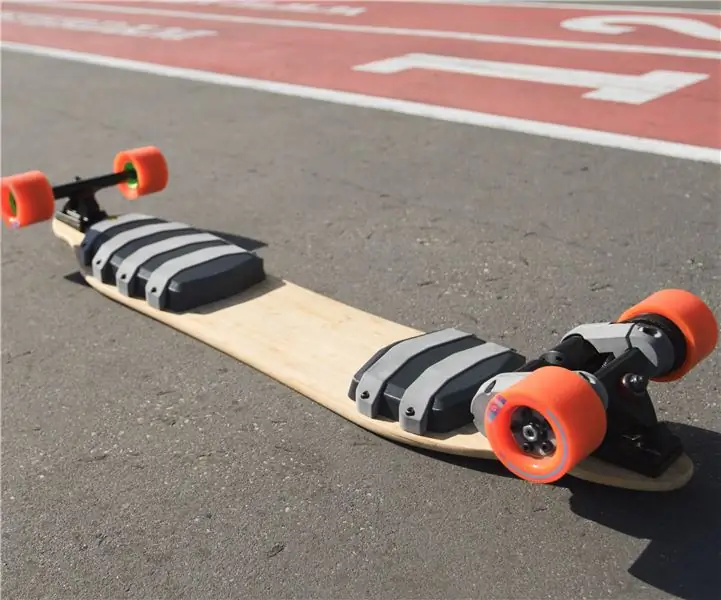
Innehållsförteckning:
2025 Författare: John Day | [email protected]. Senast ändrad: 2025-01-23 15:11
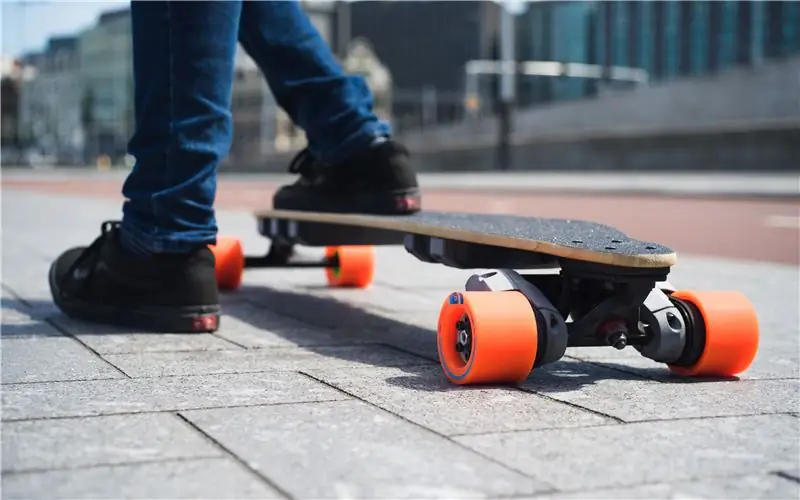
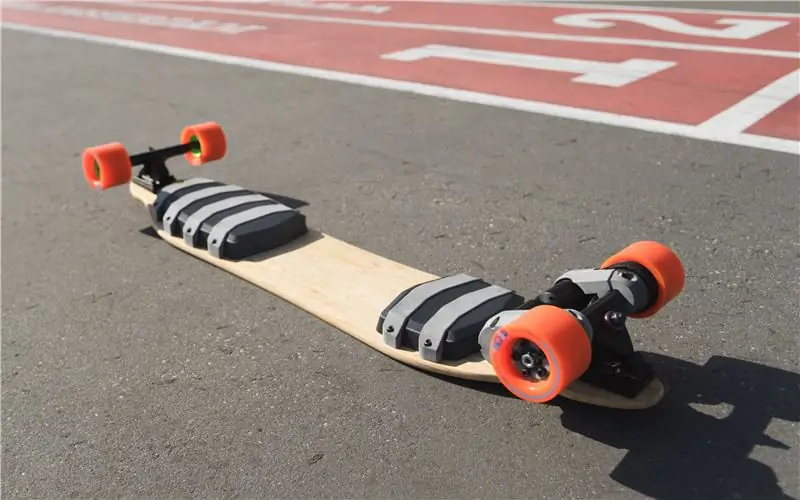
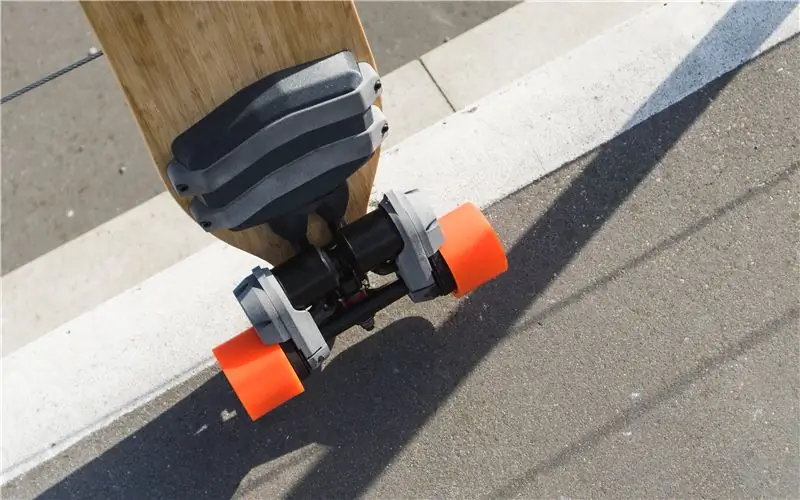
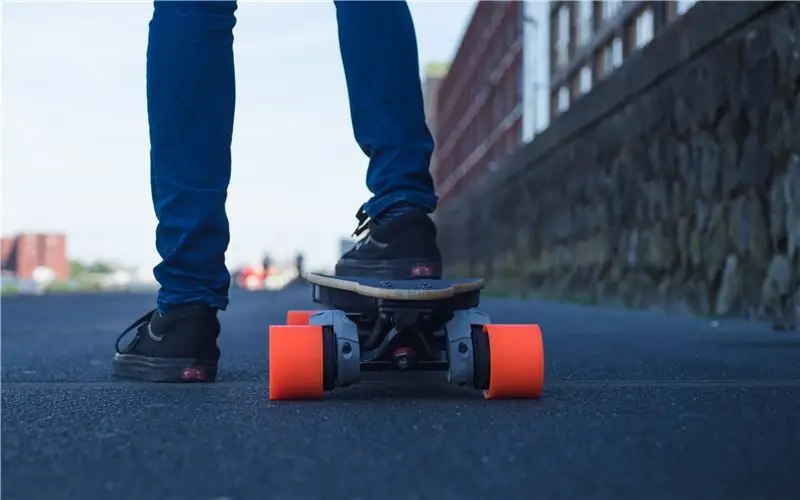
Denna instruktionsbok är en översikt över byggprocessen för Fusion E-Board som jag designade och byggde när jag arbetade på 3D Hubs. Projektet fick i uppdrag att marknadsföra den nya HP Multi-Jet Fusion-tekniken som erbjuds av 3D-hubbar och visa upp flera 3D-utskriftstekniker och hur de effektivt kan kombineras.
Jag konstruerade och byggde en elmotoriserad longboard, som kan användas för korta till måttliga resor eller kombineras med kollektivtrafik för att erbjuda ett mycket bredare reseavstånd. Den har hög toppfart, är mycket manövrerbar och bärs lätt när den inte används.
Steg 1: Designprocess
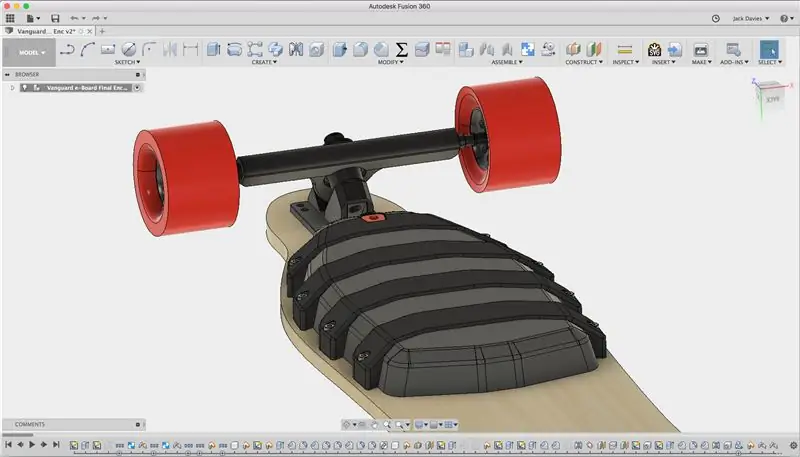
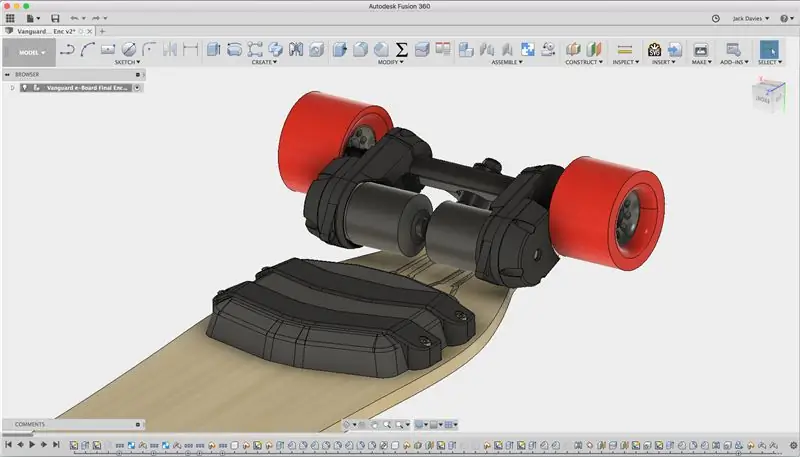
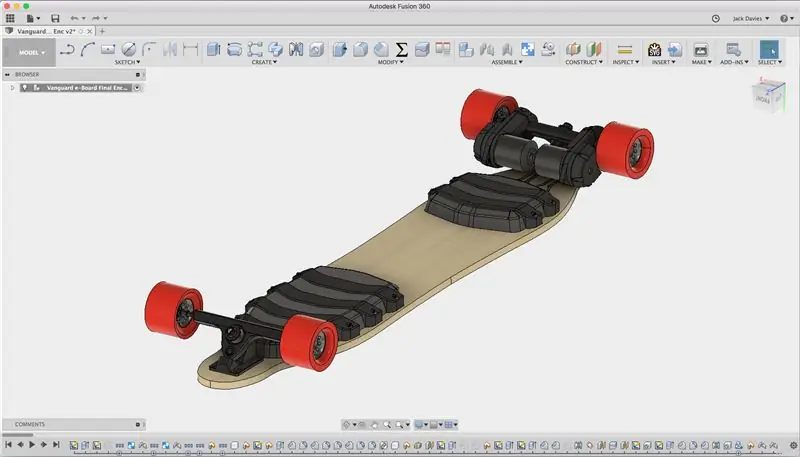
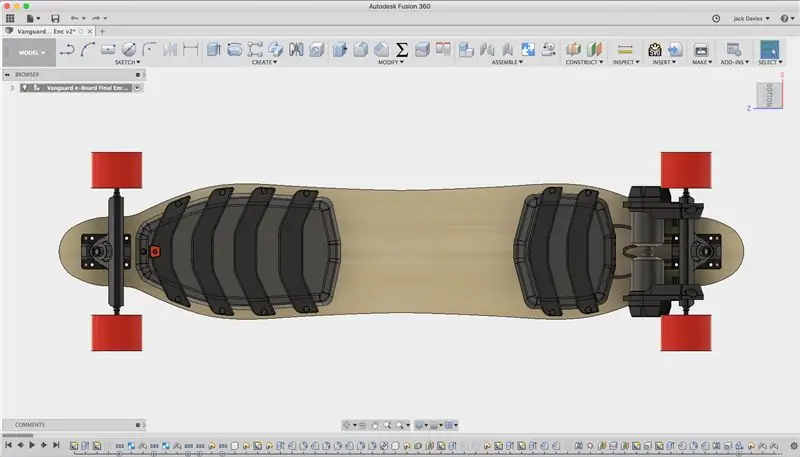
Jag startade projektet med att identifiera de viktigaste standardkomponenterna i longboard; lastbilar, däck och hjul. Dessa var från hylldelarna så jag använde dessa som utgångspunkt för designen. Det första steget var att designa drivlina, detta inkluderar motorfästen, växelinställningar och inkluderade några ändringar av lastbilarna. Storleken och positionen på motorfästena skulle diktera storleken och placeringen av kapslingarna så det var viktigt att detta slutfördes först. Jag beräknade önskad topphastighet och vridmomentkrav som sedan gjorde det möjligt för mig att välja motorer och batteri för brädet. Växlingsförhållandet beräknades också och remskivans storlek valdes, tillsammans med drivremslängden. Detta gjorde det möjligt för mig att räkna ut rätt storlek på motorfästen som säkerställde ett väl spänt bälte.
Nästa steg var att designa batteri- och hastighetsregulator (ESC) kapslingar. Det valda däcket består huvudsakligen av bambu så är ganska flexibelt och böjer sig väsentligt i mitten. Detta har fördelar med att vara bekväm att åka, eftersom det absorberar stötarna på vägen och inte överför dem till ryttaren. Detta betyder dock också att ett delat hölje behövs för att rymma batteriet och elektroniken, eftersom ett hölje i full längd inte skulle kunna böja sig med kortet och skulle komma i kontakt med marken under drift. De elektroniska varvtalsregulatorerna (ESC) placerades närmast motorerna på grund av elektriska begränsningar. Eftersom motorerna är anslutna via lastbilarna ändras positionen under svängar, så kåpan måste utformas för att möjliggöra frigöring av motorerna.
Batterisystemet placerades i andra änden av däcket och rymde elektroniken relaterad till ström. Detta inkluderade batteripaketet, bestående av 20 litiumjon 18650 celler, batterihanteringssystemet, på/av -omkopplare och laddningsuttag.
Jag använde Autodesk Fusion360 för hela designprocessen, den här programvaran gjorde det möjligt för mig att snabbt modellera komponenter inuti huvudenheten som påskyndade utvecklingstiden avsevärt. Jag använde också simuleringsfunktionerna i Fusion360 för att säkerställa att delarna skulle vara tillräckligt starka, särskilt motorfästena. Detta gjorde det möjligt för mig att faktiskt minska storleken på fästena eftersom jag kunde verifiera kraven på styrka och avböjning och ta bort material samtidigt som jag behåller en lämplig säkerhetsfaktor. Efter att designprocessen var klar var det mycket enkelt att exportera de enskilda delarna för 3D -utskrift.
Steg 2: Drivlina
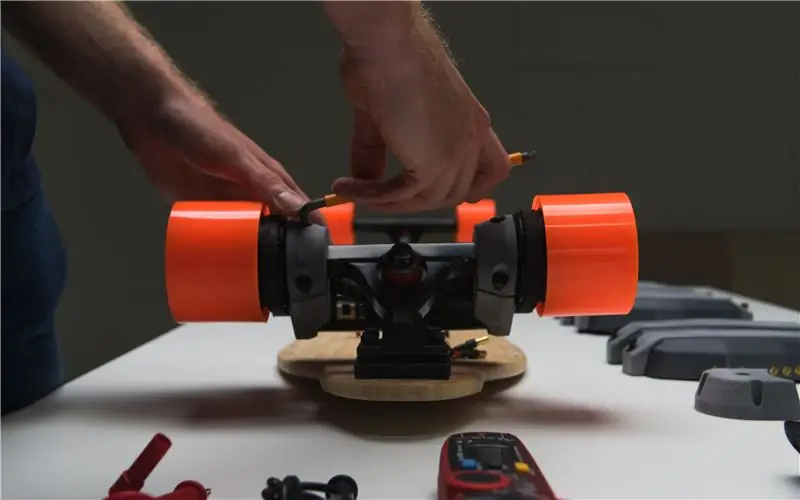
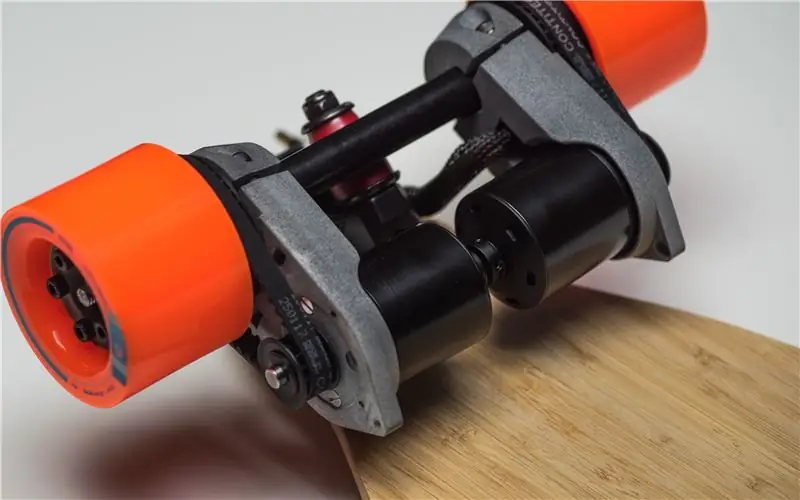
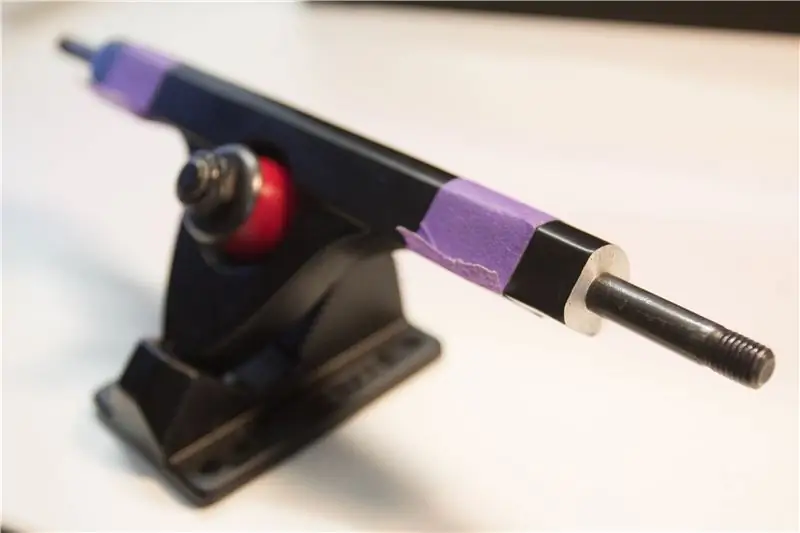
Jag slutförde byggandet av drivlina först för att säkerställa lämpligt spelrum för elektronikhöljet. Jag valde Calibertruckar att använda eftersom de har en fyrkantig profil som var perfekt för att klämma fast motorfästena. Axeln var dock något för kort för att de två motorerna skulle kunna användas på samma lastbil, så jag behövde förlänga detta för att hjulen skulle passa.
Jag uppnådde detta genom att skära ner en del av aluminium lastbilshängarkroppen och avslöja mer av stålaxeln. Jag skar sedan ner det mesta av axeln och lämnade cirka 10 mm som jag sedan kunde trä med en M8 -munstycke.
En kopplare kan sedan skruvas fast och en annan gängad axel läggas till som effektivt förlänger axeln. Jag använde Loctite 648 fästmassa för att permanent säkra kopplingen och den nya axeln för att säkerställa att den inte skulle skruvas loss under användning. Detta gjorde att de två motorerna kunde passa på lastbilen och gav gott om utrymme för hjulen.
Drivlinan trycktes främst med HP Multi-Jet Fusion-teknik för att säkerställa styvhet och styrka vid hög acceleration och bromsning, där de största krafterna skulle överföras.
En speciell remskiva utformades för att låsa fast i bakhjulen, som sedan anslöts till motorhjulet med ett HTD 5M -bälte. Ett 3D -tryckt omslag lades till för att ge skydd åt remskivanordningen.
Steg 3: Ribbskåp
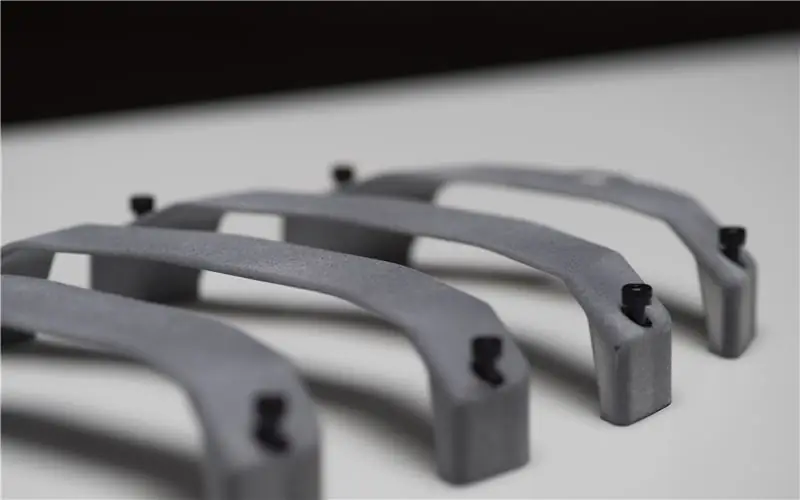
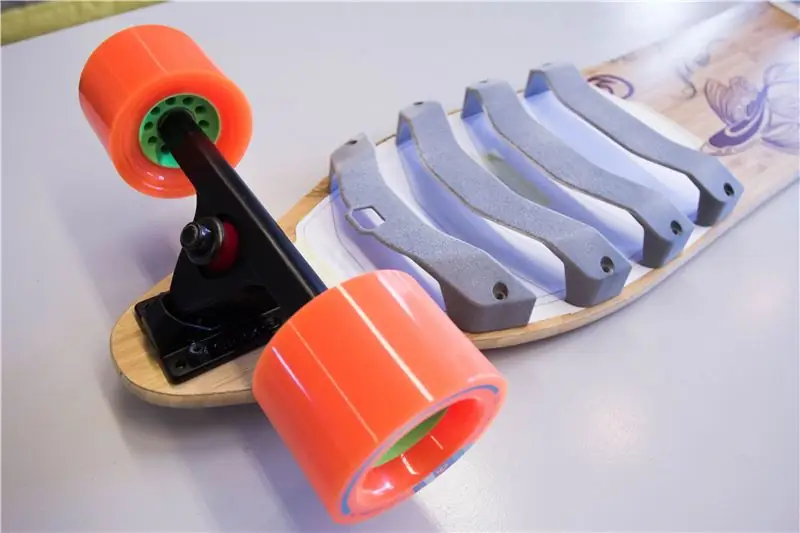
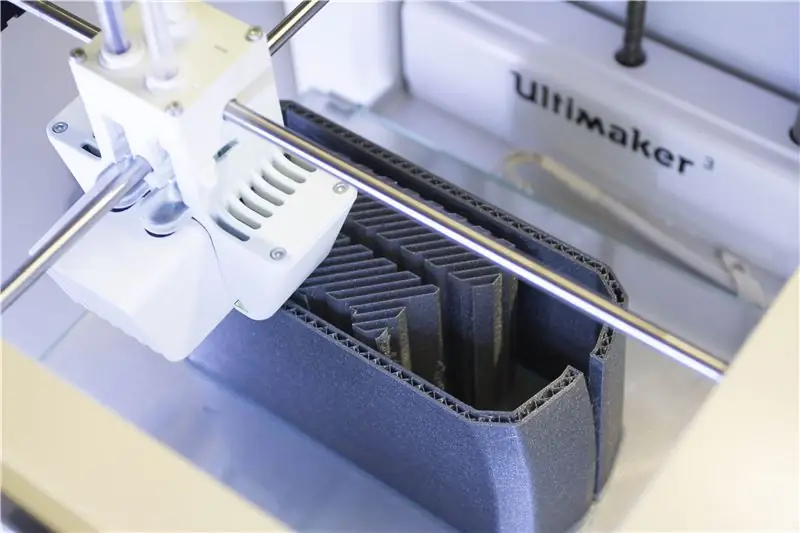
Ett av de viktigaste designbesluten jag tog var att separera höljena, vilket resulterade i ett rent utseende och möjliggjorde det flexibla däcket att fungera utan extra styvhet från höljena. Jag ville förmedla de funktionella aspekterna av HP Multi Jet Fusion -tekniken, så jag bestämde mig för att FDM skriva ut huvuddelen av höljena vilket minskade kostnaderna och använde sedan HP -delarna för att stödja och klämma fast dem på däcket. Detta gav en intressant estetik samtidigt som den var mycket funktionell.
De FDM -tryckta höljena delades i hälften för att underlätta utskriften eftersom stödmaterial kunde elimineras från utsidan. Splitlinjen placerades noggrant för att säkerställa att den doldes av HP -delen när den klämdes fast på brädet. Hål för motoranslutningarna lades till och guldpläterade kulanslutningar limmades på plats
Gängade insatser var inbäddade i bambudäcket för att säkra höljena på brädet och slipades i linje med brädans yta för att säkerställa att det inte fanns något mellanrum mellan däcket och höljet.
Steg 4: Elektronik
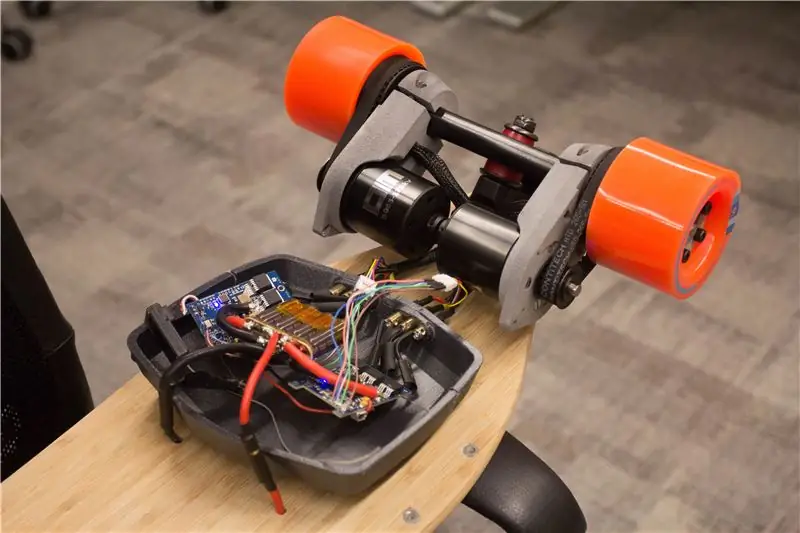
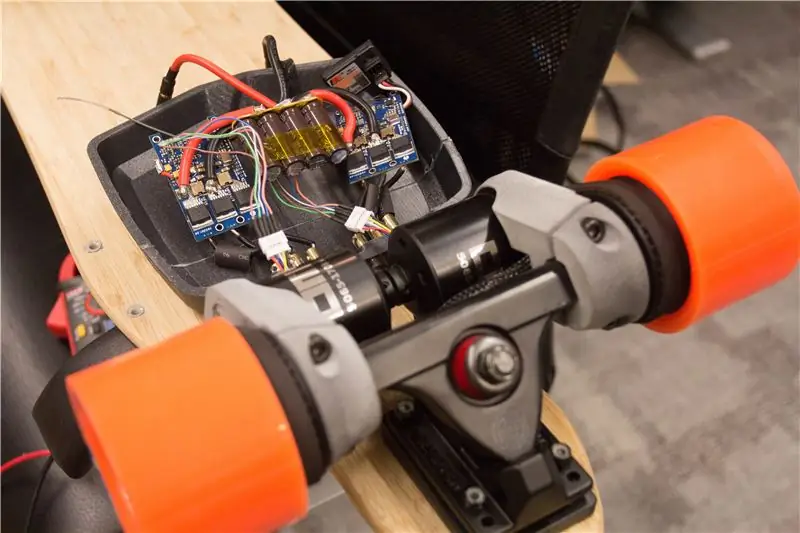
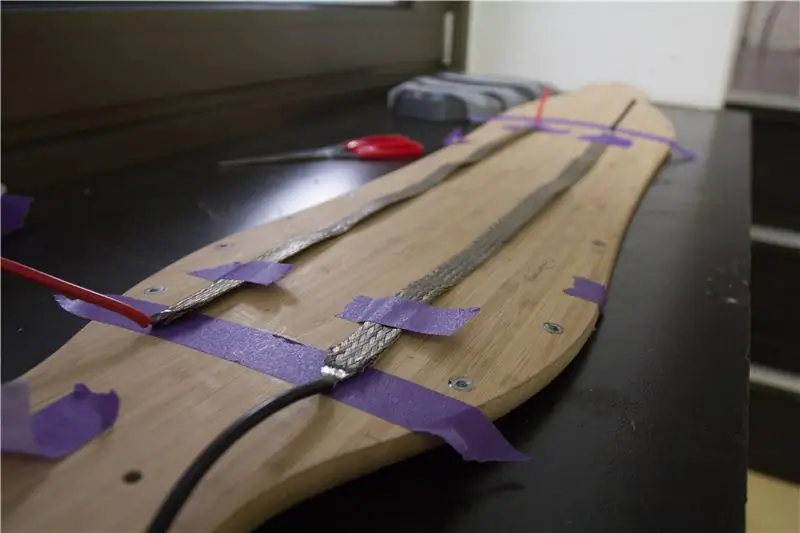
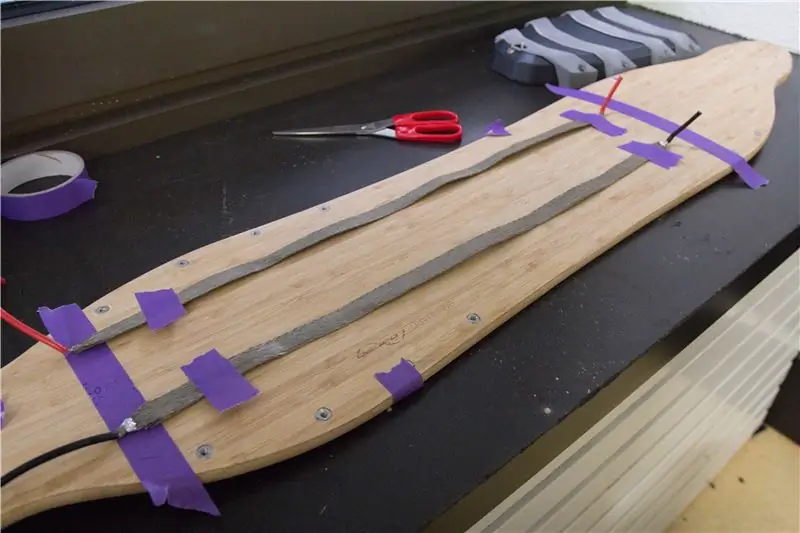
Elektroniken valdes noggrant för att säkerställa att tavlan var kraftfull men också intuitiv att använda. Detta kort kan potentiellt vara farligt om det skulle uppstå fel, så tillförlitlighet är en mycket viktig faktor.
Batteripaketet består av 20 individuella 18650 litiumjonceller som är punktsvetsade för att bilda ett 42v-förpackning. 2 celler svetsas parallellt och 10 i serie; cellerna jag använde var Sony VTC6. Jag använde en punktsvetsare för att svetsa nickelflikarna för att bilda förpackningen, eftersom lödning skapar för mycket värme som kan skada cellen.
Strömmen från batterihöljet överfördes till hastighetsreglerboxen med en platt flätad kabel som lades strax under grepptejpen på ovansidan av däcket. Detta gjorde att kablarna kunde "döljas" och eliminerade behovet av att köra kablar på undersidan vilket skulle ha sett ful ut.
Eftersom detta är ett dubbelmotorkort krävs två hastighetsregulatorer för att oberoende styra varje motor. Jag använde VESC -hastighetsregulatorn för denna konstruktion, som är en styrenhet speciellt utformad för elektriska skateboards vilket gör den mycket tillförlitlig för denna användning.
De motorer som används är 170kv 5065 utlöpare som kan producera 2200W vardera, vilket är mycket kraft för detta kort. Med den nuvarande växellådan är brädans maxhastighet cirka 35 MPH och accelererar mycket snabbt.
Det sista steget var att skapa en fjärrkontroll för att styra kortet. Ett trådlöst system föredrogs på grund av den enklare driften. Det var emellertid viktigt att säkerställa hög tillförlitlighet för överföringen, eftersom kommunikationsfall skulle kunna ha allvarliga säkerhetsproblem, särskilt vid höga hastigheter. Efter att ha testat några radioöverföringsprotokoll bestämde jag mig för att 2,4 GHz radiofrekvens skulle vara den mest tillförlitliga för detta projekt. Jag använde en RC -sändare från hyllan, men minskade avsevärt storleken genom att överföra elektroniken till ett litet handhållet fodral som var 3D -tryckt.
Steg 5: Färdig tavla och kampanjvideo
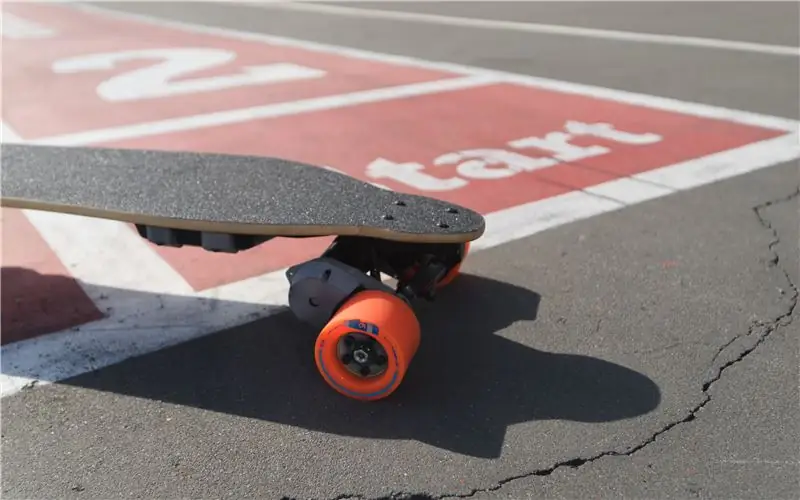
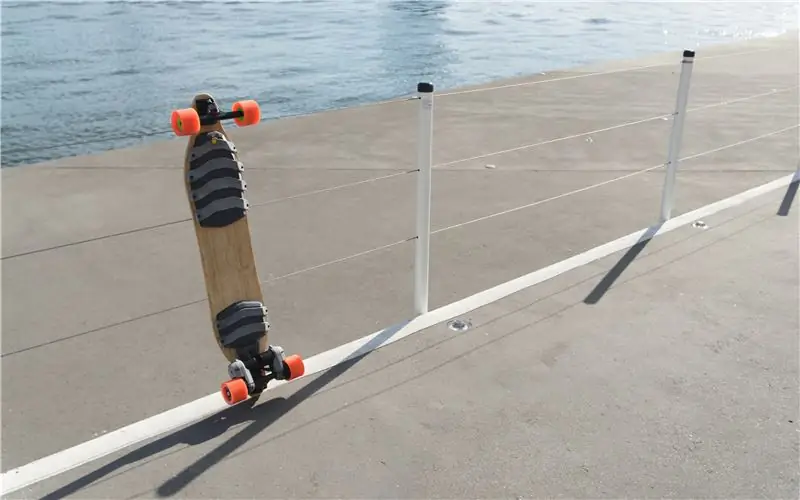
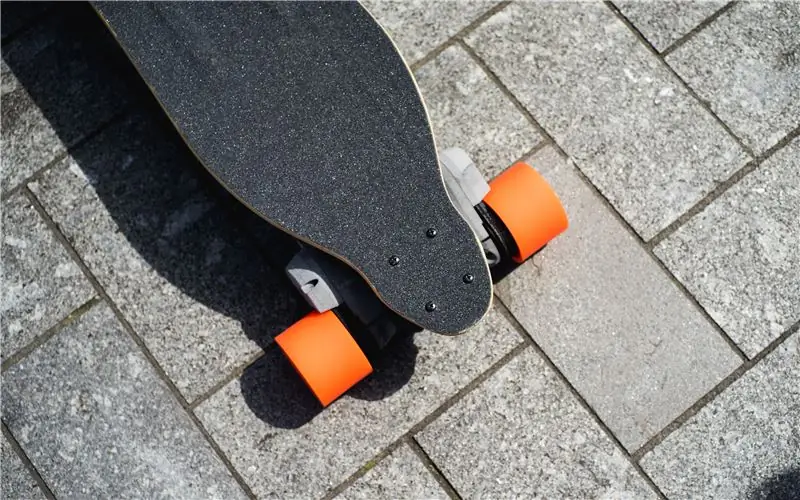
Projektet är nu klart! Vi skapade en ganska fantastisk video av tavlan i aktion, du kan kolla in den nedan. Stort tack till 3D Hubs för att jag fick göra detta projekt - kolla in dem här för alla dina 3D -utskriftsbehov! 3dhubs.com
Rekommenderad:
Styr kraftfull elektrisk skateboard elcykel 350W likströmsmotor med Arduino och BTS7960b: 9 steg
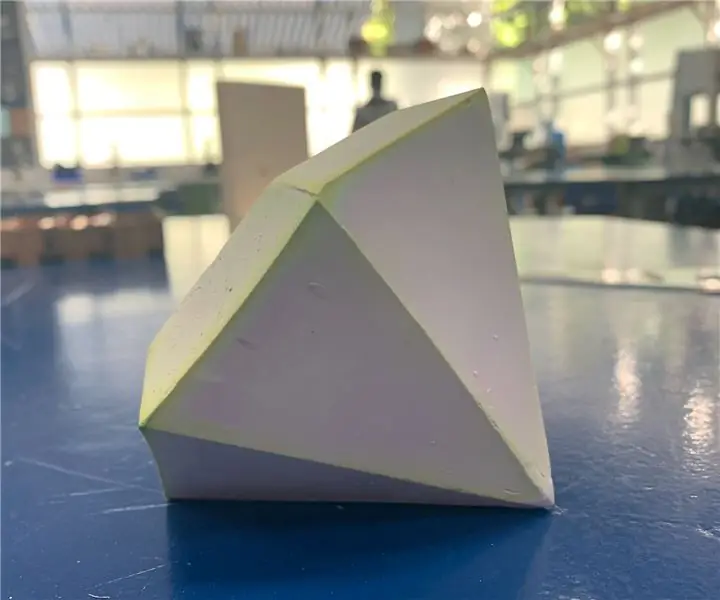
Styr kraftfull elektrisk skateboard E-cykel 350W likströmsmotor med Arduino och BTS7960b: I denna handledning kommer vi att lära oss hur man styr en likströmsmotor med Arduino och DC-drivrutin bts7960b. Motorn kan vara en 350W eller bara en liten leksak arduino likströmsmotor så länge dess effekt inte överstiger BTS7960b -drivrutinen Max ström. Se videon
Speedboard: elektrisk skateboard: 5 steg
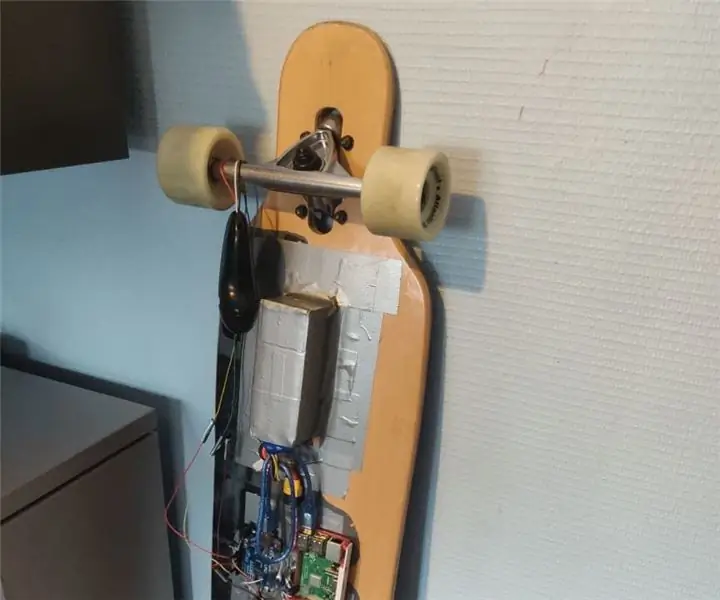
Speedboard: Electric Skateboard: Hej! Jag är en MCT College Student från Howest i Belgien. Idag kommer jag att ge dig en steg -för -steg -guide om hur du gör en elektrisk skateboard med en hallonpi och arduino. Jag blev inspirerad att göra detta projekt av en berömd youtuber som heter Casey Neistat .
Vägmätare för elektrisk skateboard: 5 steg
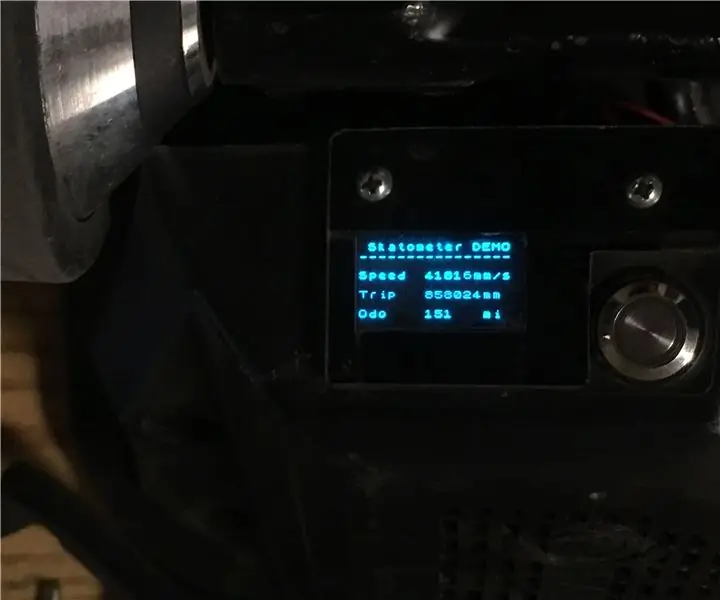
Elektrisk Skateboard Vägmätare: Introduktion De flesta avancerade elektriska skateboardarna runt tusen dollar kommer med en telefonapp som visar skateboardinformation i realtid och tyvärr kommer de mer kostnadseffektiva skateboards från Kina inte med dem. Så varför inte
Tryckkänslig elektrisk skateboard: 7 steg
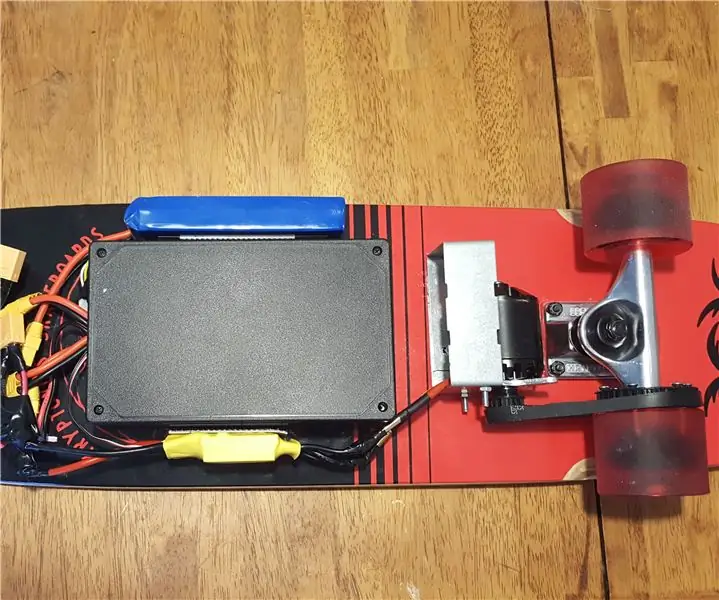
Tryckkänslig elektrisk skateboard: Denna instruerbara skapades för att uppfylla projektkravet för Makecourse vid University of South Florida (www.makecourse.com). Följande instruktioner kommer att förklara byggprocessen för en elektrisk skateboard som använder ett tryck
DIY elektrisk skateboard: 14 steg (med bilder)
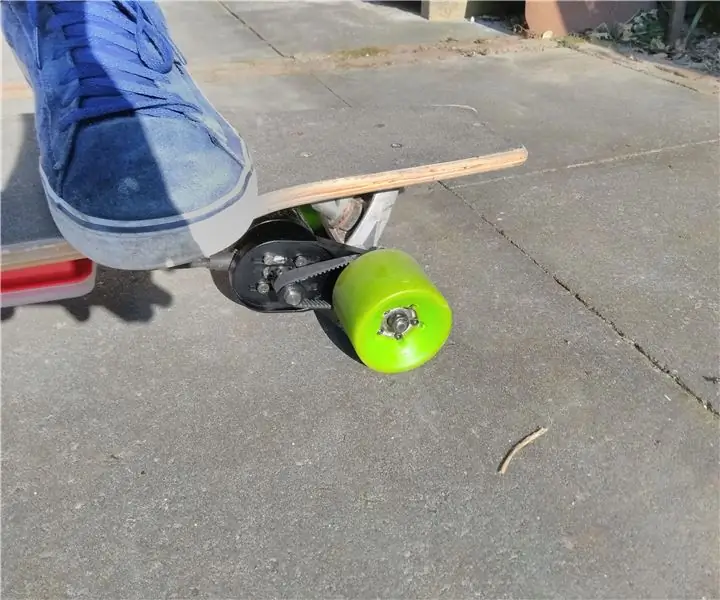
Diy Electric Skateboard: Efter 2 års forskning har jag byggt min första elektriska skateboard. Eftersom jag har sett en instruktion om hur man bygger din egen elektriska skateboard har jag varit kär i DIY elektriska skateboards. Att göra din egen elektriska skateboard är en form av