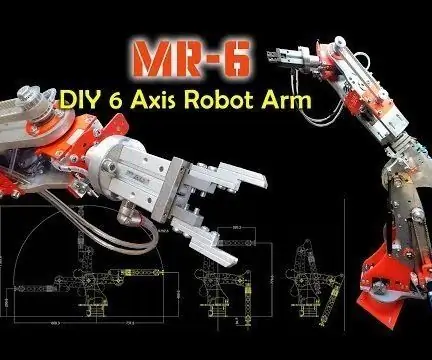
Innehållsförteckning:
2025 Författare: John Day | [email protected]. Senast ändrad: 2025-01-23 15:11
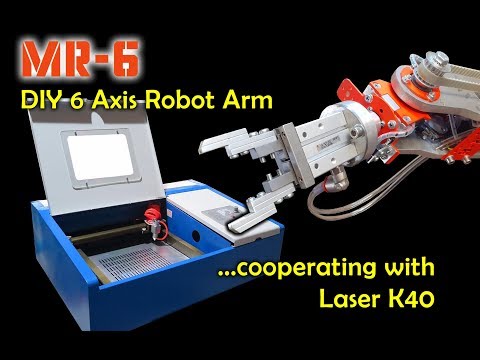
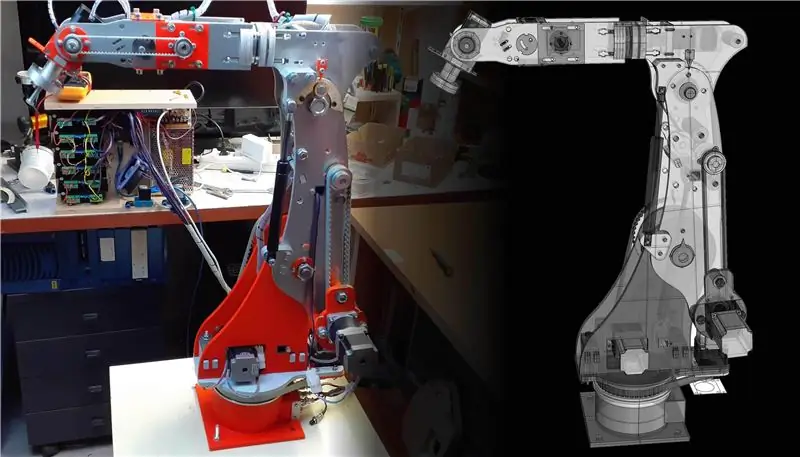
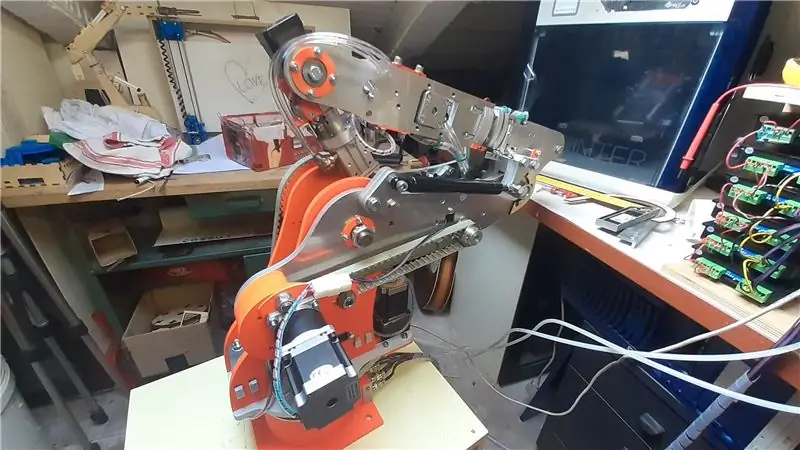
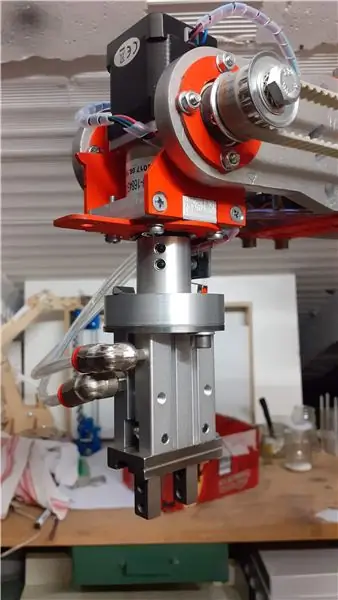
Efter mer än ett års studier, prototyper och olika misslyckanden lyckades jag bygga en järn / aluminiumrobot med 6 frihetsgrader som styrs av stegmotorer.
Den svåraste delen var designen eftersom jag ville uppnå tre grundläggande mål:
- Låg realiseringskostnad
- Enkel montering även med lite utrustning
- Bra precision vid rörelse
Jag konstruerade 3D -modellen med Rhino flera gånger tills (enligt min mening) en bra kompromiss som uppfyller de tre kraven.
Jag är ingenjör och innan det här projektet hade jag ingen erfarenhet av robotik så en person som är mer erfaren än jag kunde hitta designfel i det jag gjorde men jag kan fortfarande säga att jag är nöjd med det slutresultat jag uppnådde.
Tillbehör
för mer info besök min personliga blogg
Steg 1: CAD -design
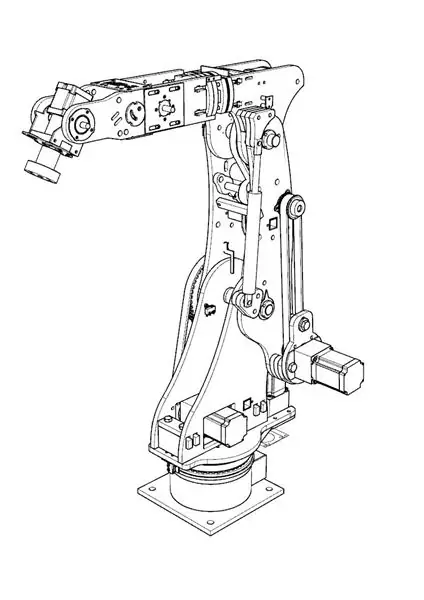
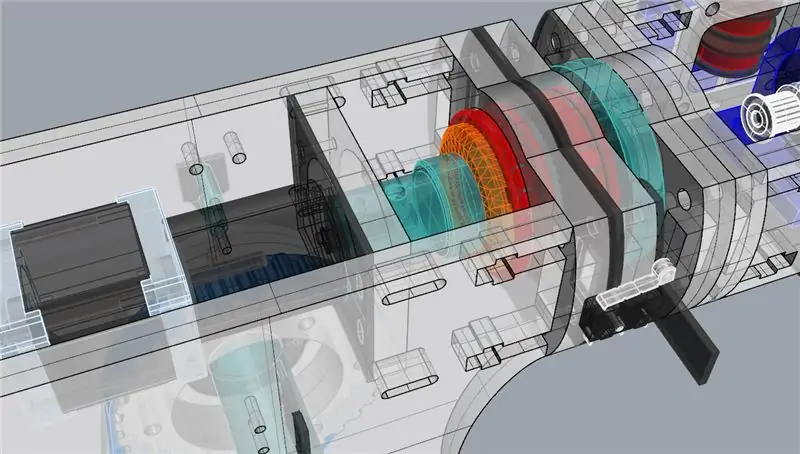
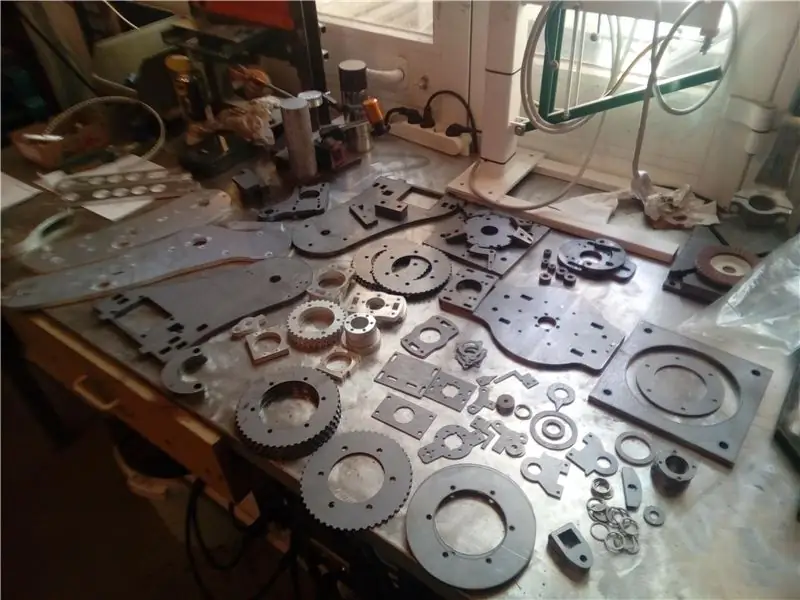
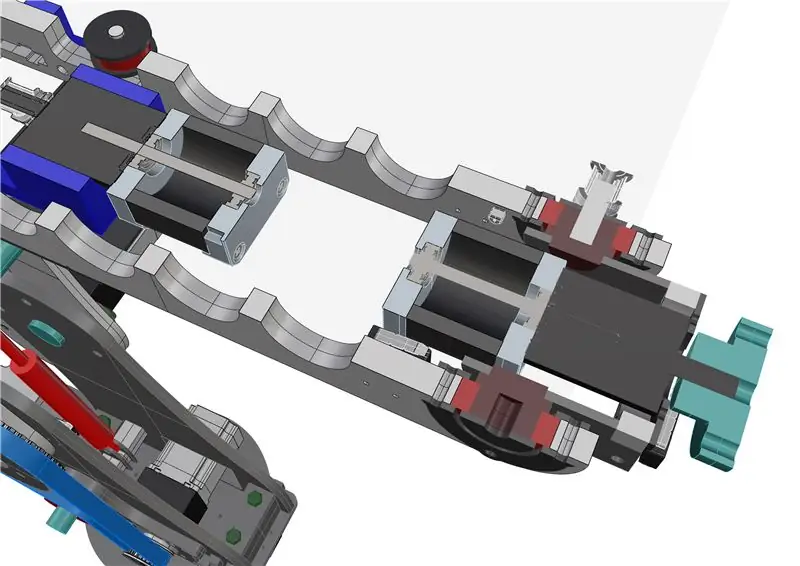
Innan jag kom fram till den slutliga modellen konstruerade jag minst 8 olika prototyper med olika överföringssystem men ingen kunde uppfylla de tre kraven som beskrivs ovan.
Genom att sätta ihop de mekaniska lösningarna för alla gjorda prototyper (och även acceptera vissa kompromisser) kom den slutliga modellen fram. Jag räknade inte timmarna jag spenderade framför CAD men jag kan försäkra er om att de var riktigt många.
En aspekt att tänka på i konstruktionsstadiet är att även ett enda gram som läggs till i slutet av robotens handled multipliceras på bekostnad av motorns vridmomentmotstånd vid basen och därför läggs mer vikt till och ju mer motorerna måste beräknas för att klara ansträngningen.
För att "hjälpa" motorerna att klara påfrestningarna applicerade jag gaskolvar på 250N och 150N.
Jag tänkte minska kostnaderna genom att skapa roboten med laserskurna järnplattor (C40) och aluminium med tjocklekar från 2, 3, 5, 10 mm; laserskärning är mycket billigare än 3D -metallfräsning.
Efter att ha utformat varje enskild komponent gjorde jag bitarnas former i.dxf och skickade dem till skärcentret. Resten av komponenterna gjordes av mig själv vid svarven.
Steg 2: Förberedelse och montering
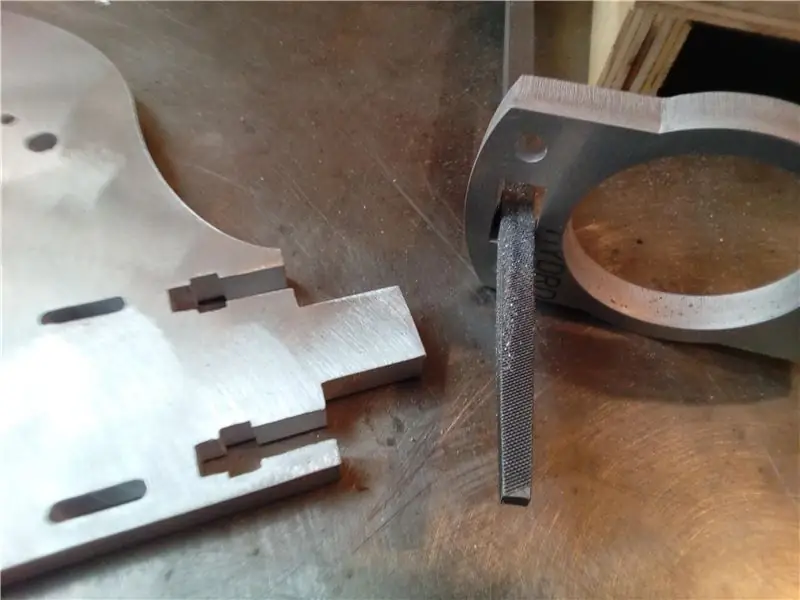
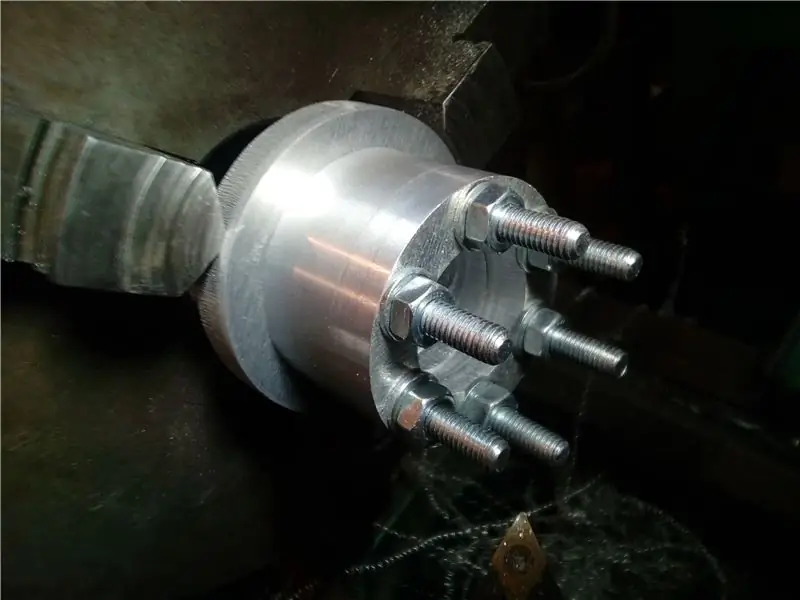
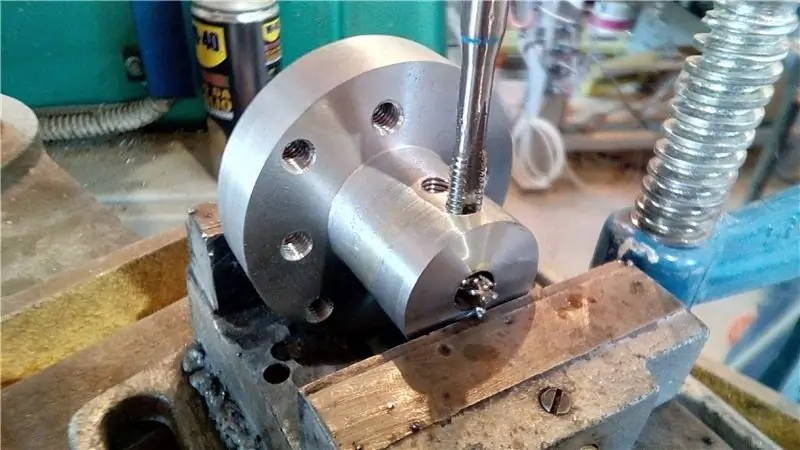
Äntligen är det dags att smutsiga händerna (det är det jag gör bäst) …
Konstruktionsfasen har tagit bort många timmars arbete för förberedelse av bitarna, manuell arkivering av hålen, lederna, gängorna och vridningen av naven. Det faktum att jag har konstruerat varenda komponent för att kunna arbeta med bara några arbetsverktyg har lett till att jag inte har några stora överraskningar eller mekaniska problem.
Det viktigaste är att inte skynda sig för att avsluta saker utan att vara noggrann och följa varje rad i projektet, improvisering i detta skede leder aldrig till bra resultat.
Att inse lagersätena är extremt viktigt eftersom varje led vilar på dem och till och med ett litet spel på några få procent kan äventyra projektets framgång.
Jag fann mig själv behöva göra om stiften eftersom jag med svarven hade tagit bort cirka 5 cent mindre än lagerhålet och när jag försökte montera det var spelet påtagligt uppenbart.
Verktygen jag använde för att förbereda alla bitar är:
- borrpress
- kvarn / dremel
- slipsten
- manuell fil
- svarv
- Engelska nycklar
Jag förstår att inte alla kan ha en svarv hemma och i det här fallet kommer det att vara nödvändigt att beställa bitarna till ett specialiserat center.
Jag hade konstruerat bitarna för att laserskäras med de lite mer överflödiga lederna för att kunna perfekta dem för hand eftersom lasern, hur exakt den än är, genererar ett koniskt snitt och det är viktigt att överväga det.
Arbeta med filen för hand varje led jag gjorde för att skapa en mycket exakt koppling mellan delarna.
Till och med hålen i lagersätena hade jag gjort mindre och sedan breddat dem för hand med dremel och mycket (men verkligen mycket) tålamod.
Alla trådar som jag gjorde för hand på borrpressen eftersom den maximala vinkelrättheten mellan instrumentet och stycket erhålls. Efter att ha förberett varje bit har det efterlängtade sanningens ögonblick kommit, hela robotens sammansättning. Jag blev förvånad över att upptäcka att varje bit passade exakt in i den andra med rätt toleranser.
Roboten är nu monterad
Innan jag gjorde något annat föredrog jag att göra några rörelsestester för att se till att motorerna är korrekt utformade. Om jag hittar problem med motorerna, särskilt deras åtdragningsmoment, kommer jag att tvingas göra om en bra del av projektet.
Så efter att ha monterat de 6 motorerna tog jag den tunga roboten till mitt vindslabb för att skicka den till de första testerna.
Steg 3: Första rörelsetester
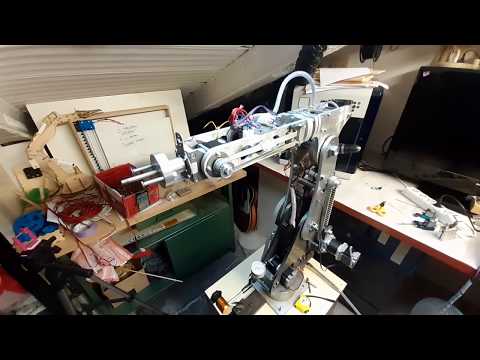
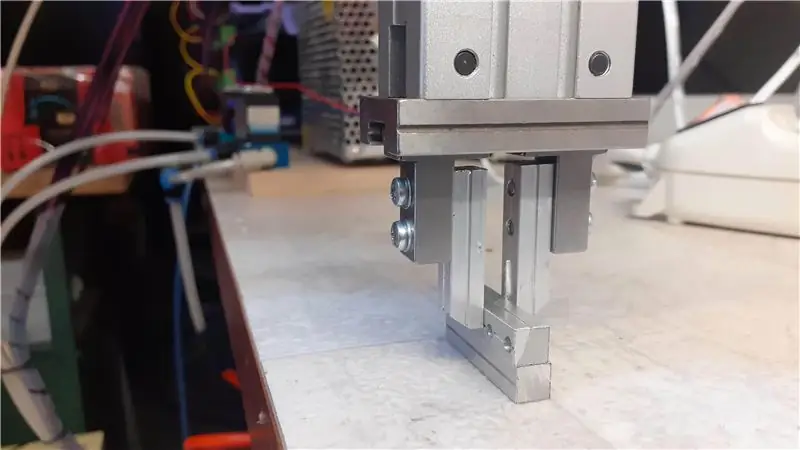
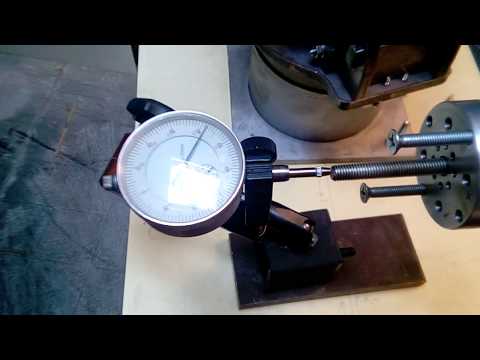
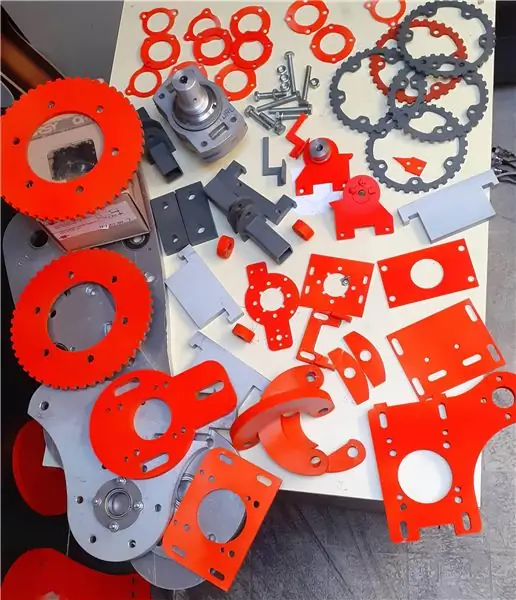
Efter att ha slutfört den mekaniska delen av roboten monterade jag snabbt elektroniken och kopplade endast kablarna till de 6 motorerna. Testresultaten var mycket positiva, lederna rör sig bra och i de förutbestämda vinklarna upptäckte jag ett par lättlösta problem.
Det första problemet gäller gemensamt nr. 3 som vid maximal förlängning överbelastade bältet för mycket och ibland orsakade förlust av steg. Lösningen på detta problem har lett mig till olika argument som vi kommer att se i nästa steg.
Det andra problemet gäller det gemensamma nr. 4, var lösningen av bältets vridning inte alltför pålitlig och genererade problem. Samtidigt började järndelarna i roboten göra små rostpunkter, så med möjligheten att lösa problemen tog jag också tillfället i akt att måla den.
Steg 4: Måla och montera igen
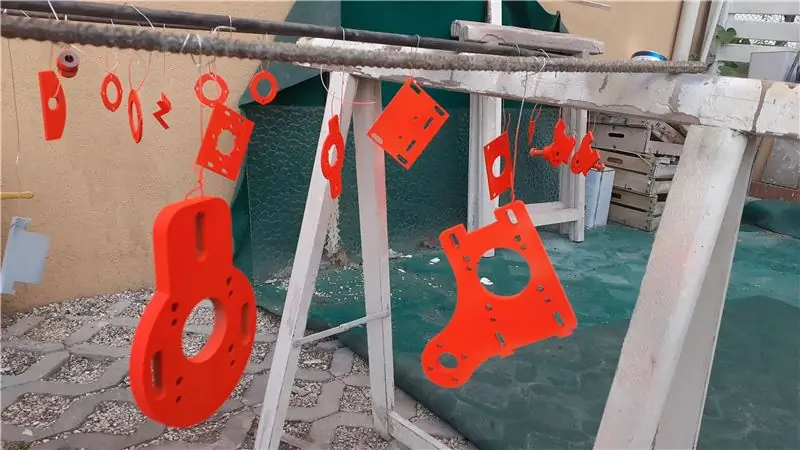
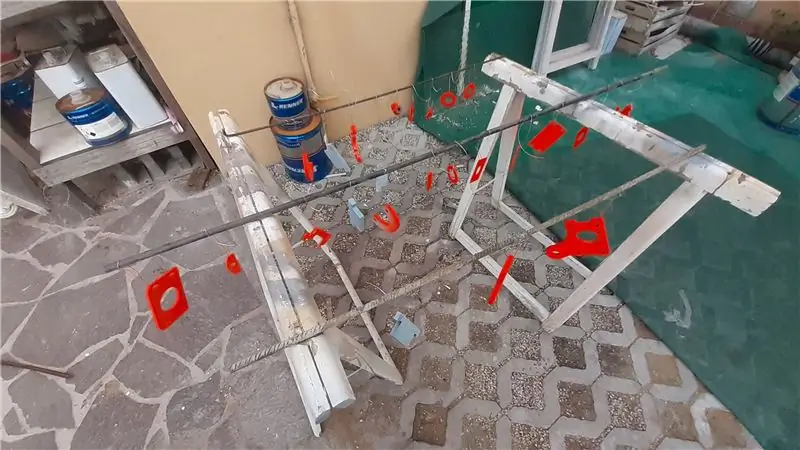
Jag gillar inte målningsfasen särskilt, men i det här fallet är jag skyldig att göra det eftersom jag älskar det ännu mindre.
På järnet lägger jag först en primer som fungerar som bakgrund för den röda fluofärgen.
Steg 5: Bug Fix N.1
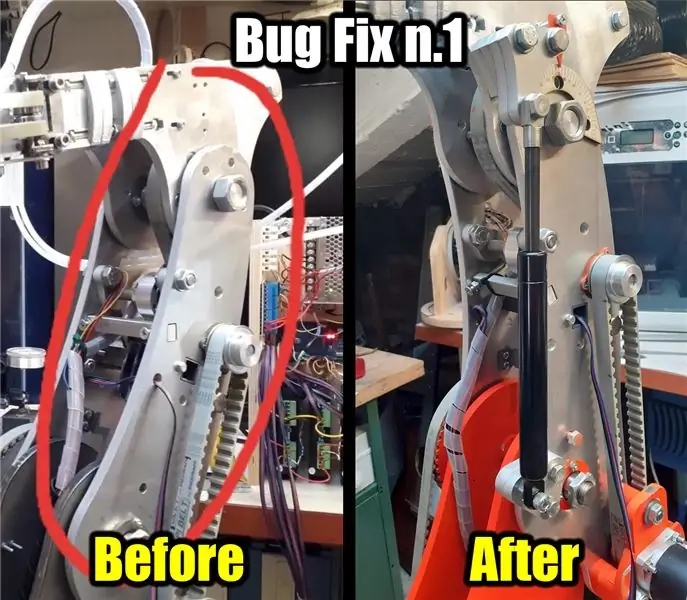
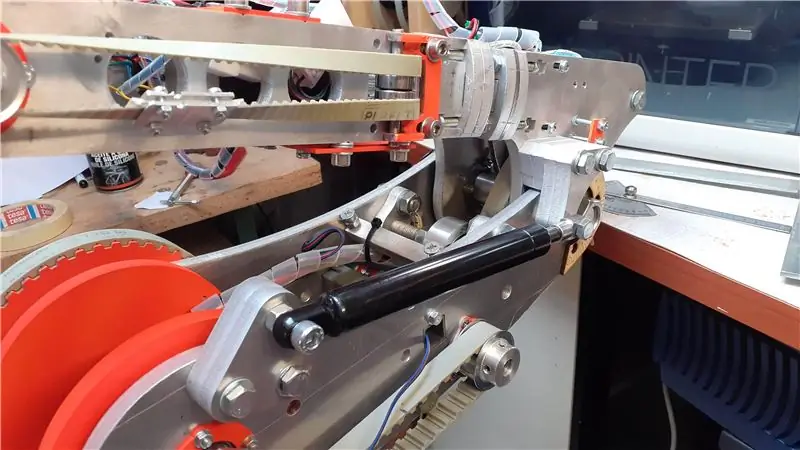
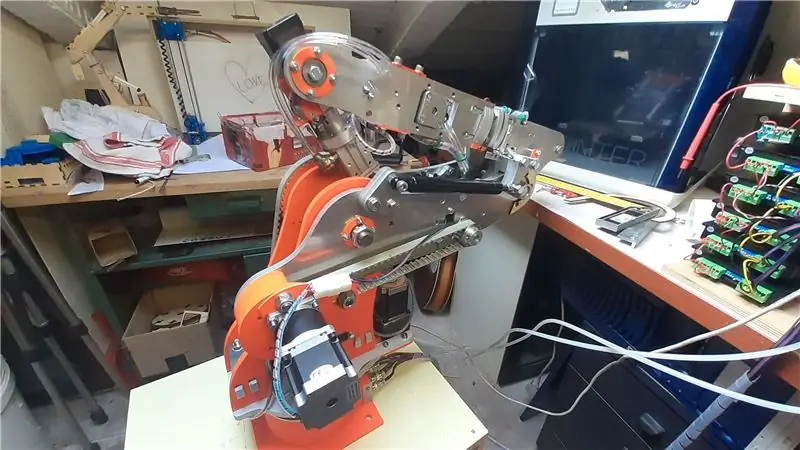
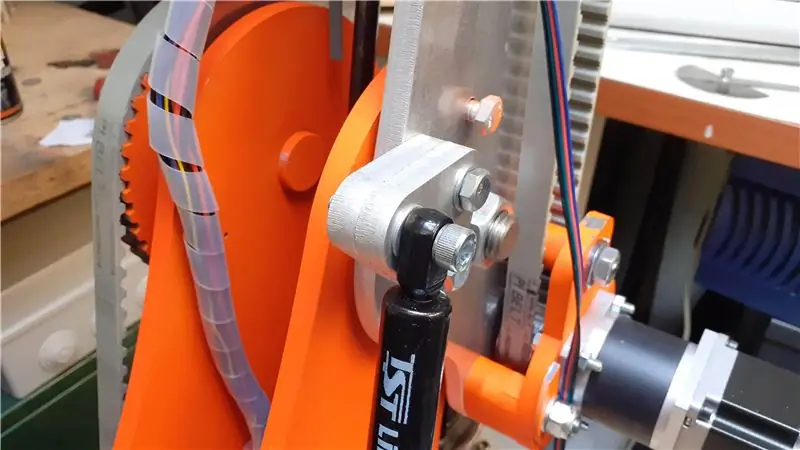
Efter testresultaten var jag tvungen att göra några ändringar för att förbättra robotens noggrannhet. Den första modifieringen gäller leden # 3 i synnerhet när den var i det mest ogynnsamma tillståndet utövade en överdriven dragkraft i bältet och följaktligen var motorn alltid under påfrestning. Lösningen var att hjälpa till genom att applicera en kraft som strider mot rotationsriktningen.
Jag tillbringade hela nätter med att fundera på vad som kan vara den bästa lösningen utan att behöva göra allt igen. Inledningsvis tänkte jag applicera en stor torsionsfjäder, men när jag letade på nätet hittade jag inget tillfredsställande så jag valde en gaskolv (som jag redan hade konstruerat för led nr 2), men jag var fortfarande tvungen att bestämma var jag skulle placera den eftersom jag hade inte tillräckligt med plats.
Jag gav upp lite estetik och bestämde mig för att det bästa stället att placera kolven var på sidan.
Jag gjorde beräkningarna av kolvens nödvändiga effekt med tanke på den punkt där den var tvungen att utöva kraften och sedan beställde jag på ebay en 150 N kolv lång 340 mm sedan konstruerade jag de nya stöden för att kunna fixa det.
Steg 6: Bug Fix N.2

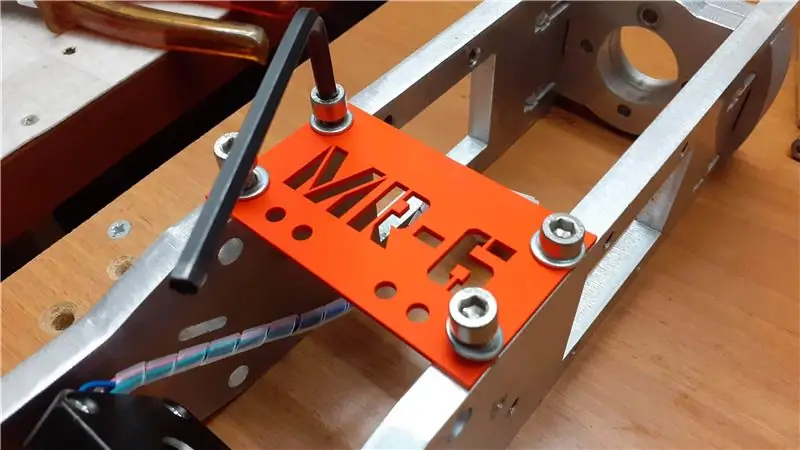
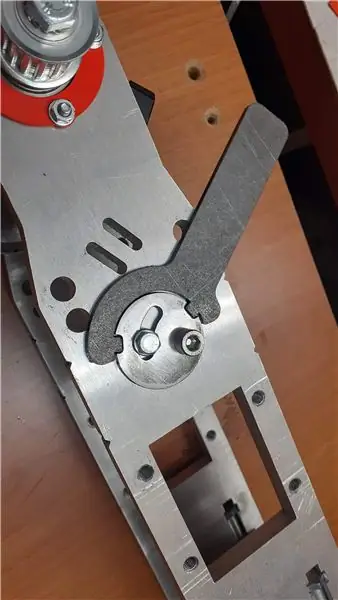
Den andra ändringen gäller gemensamt nr. 4 där jag inledningsvis hade planerat växellådan med det vridna bältet men jag insåg att utrymmena minskade och att bältet inte fungerade så bra som jag hoppades.
Jag bestämde mig för att göra om hela leden helt genom att designa axlarna för att ta emot motorn i parallell riktning i förhållande till dem. Med denna nya modifiering fungerar bältet nu korrekt och det är också lättare att spänna det eftersom jag har konstruerat ett nyckelsystem för att enkelt spänna bältet.
Steg 7: Elektronik
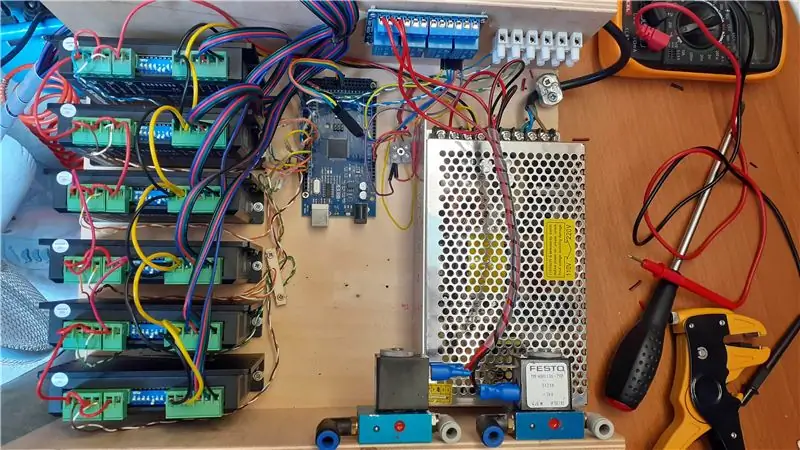
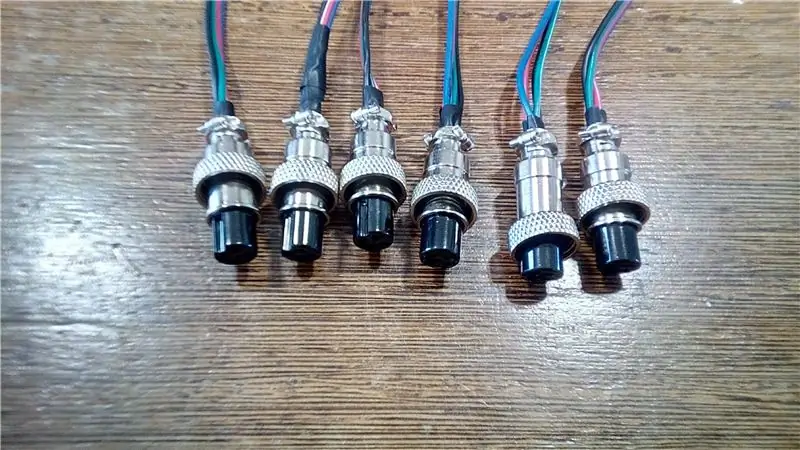
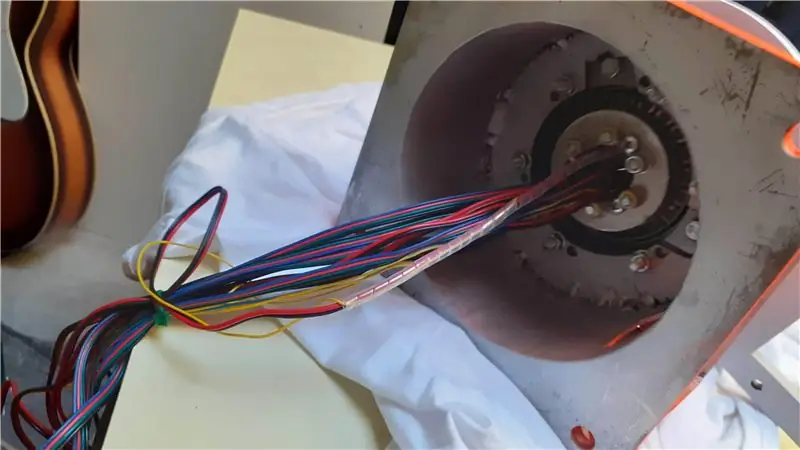
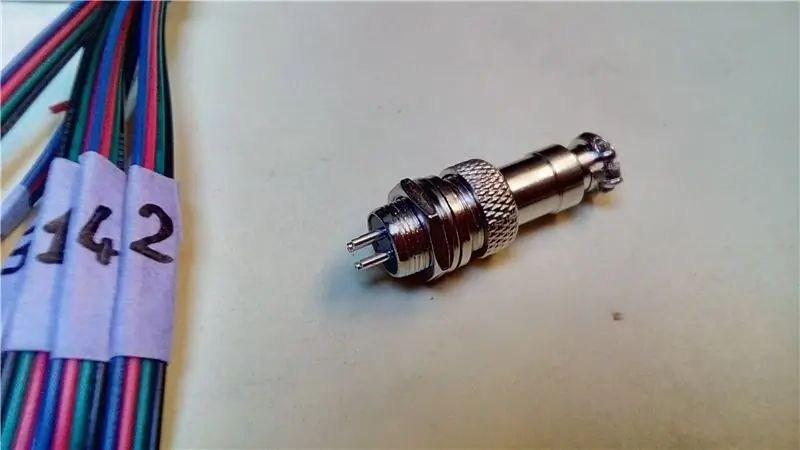
Motorstyrelektroniken är densamma som används för en klassisk 3-axlig CNC med skillnaden att det finns 3 fler drivrutiner och 3 motorer till att hantera. Alla axlar styrlogik beräknas av applikationen, elektroniken har den enda uppgiften att få instruktioner om hur många grader motorerna måste rotera så att leden inte når önskat läge.
Delarna som utgör elektroniken är:
- Arduino Mega
- n. 6 förare DM542T
- n. 4 Relè
- n. 1 24V strömförsörjning
- n. 2 magnetventiler (för pneumatisk klämma)
På Arduino laddade jag skissen som handlar om att samtidigt hantera motorernas rörelser som acceleration, retardation, hastighet, steg och maxgränser och är programmerad för att ta emot kommandon som ska utföras via seriell (USB).
Jämfört med de professionella rörelsekontrollerna som kan kosta upp till flera tusen euro, försvarar Arduino sig på ett alldeles för uppenbart för komplext sätt som det inte kan hantera, till exempel multitråden, särskilt när du måste hantera flera motorer samtidigt.
Steg 8: Programvaruöverväganden
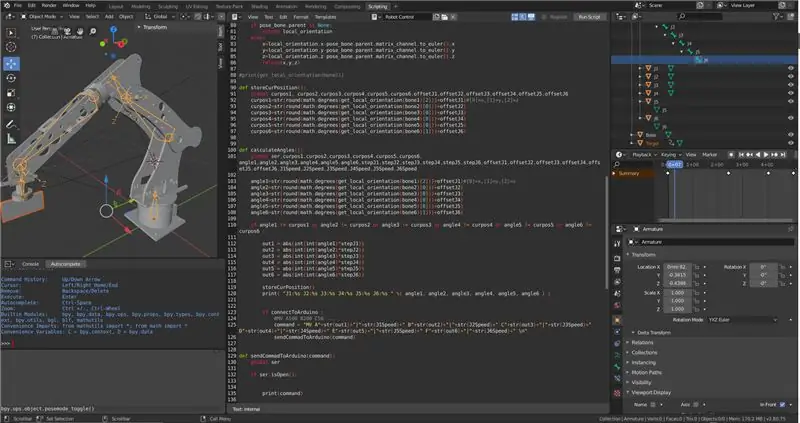
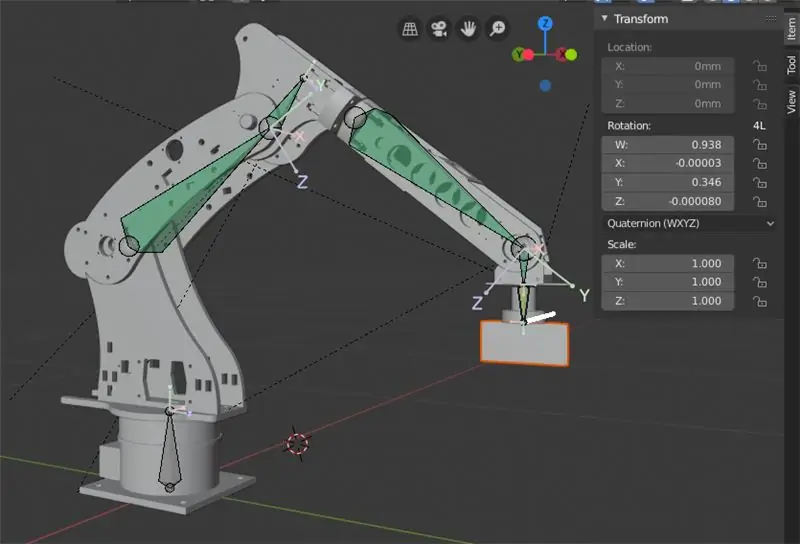
Varje robot har sin egen form och olika rörelsevinklar och kinematiken är olika för var och en av dem. För närvarande för att köra testerna använder jag programvaran från Chris Annin (www.anninrobotics.com) men matten som skrivits för hans robot passar inte perfekt till mina, faktiskt vissa områden av arbetsområdet jag inte kan nå dem eftersom beräkningarna av hörnen inte är fullständiga.
Annins programvara är bra nu för att experimentera, men jag måste börja tänka på att skriva min egen programvara som passar 100% med min robots fysik. Jag har redan börjat göra några tester med Blender och skriva Python -delen av rörelsekontrollen och det verkar vara en bra lösning, det finns några aspekter att utveckla men den här kombon (Blender + Ptyhon) är väldigt lätt att implementera, särskilt det är enkelt att planera och simulera rörelser utan att ha roboten framför dig.
Steg 9: Pneumatisk klämma

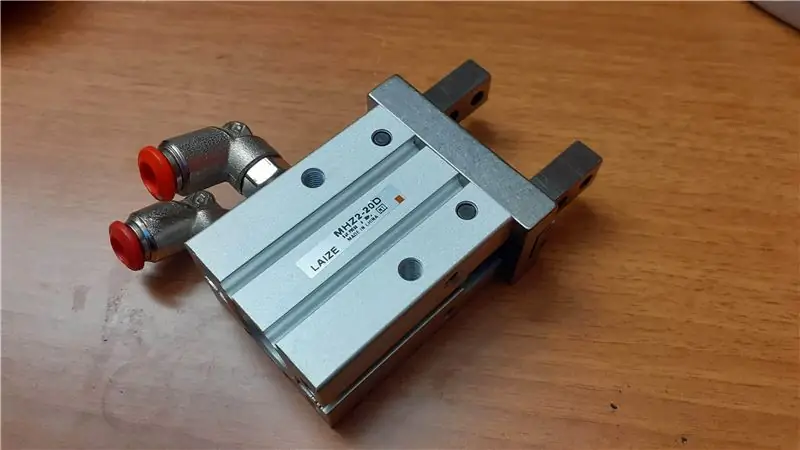
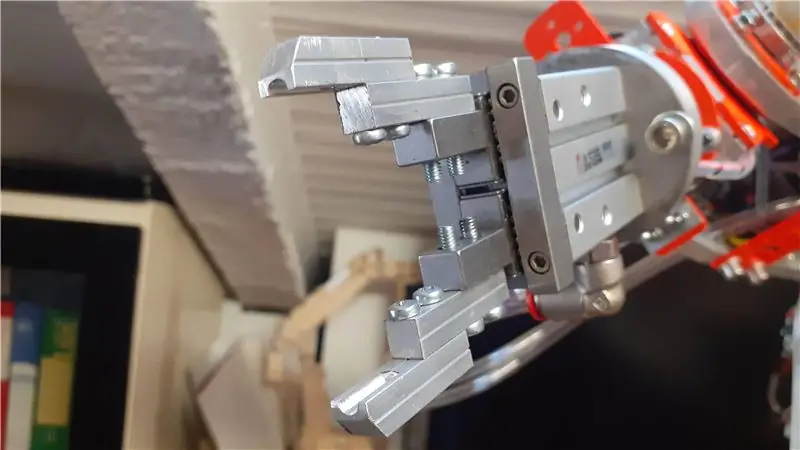
För att kunna ta föremål till roboten har jag utrustat den med en pneumatisk klämma.
Personligen gillar jag inte tång med servon, de ger mig inte mycket förtroende för tätningen så jag trodde att en pneumatisk tang som specifikt justerade trycket kunde tillgodose alla behov.
Med fyrkantiga aluminiumprofiler modifierade jag klämman för att ta både små föremål och stora föremål.
Senare, när jag hittar tid, kommer jag att samla all information om projektet så att jag kan ladda ner den.
Jag hoppas att du njöt av detta instruerbara.
Rekommenderad:
Robotarm med grip: 9 steg (med bilder)
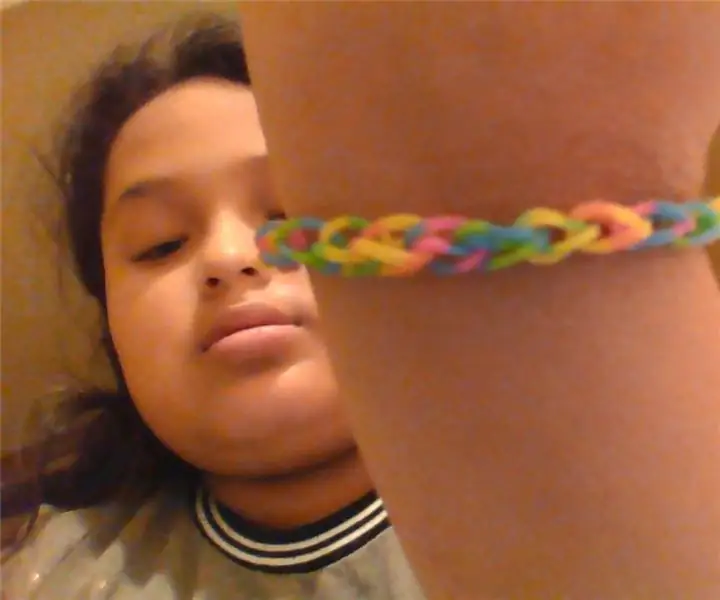
Robotarm med gripare: Att skörda citronträd anses vara hårt arbete, på grund av trädens stora storlek och också på grund av det varma klimatet i de regioner där citronträd planteras. Det är därför vi behöver något annat för att hjälpa jordbruksarbetare att slutföra sitt arbete mer
3D robotarm med Bluetooth -styrda stegmotorer: 12 steg
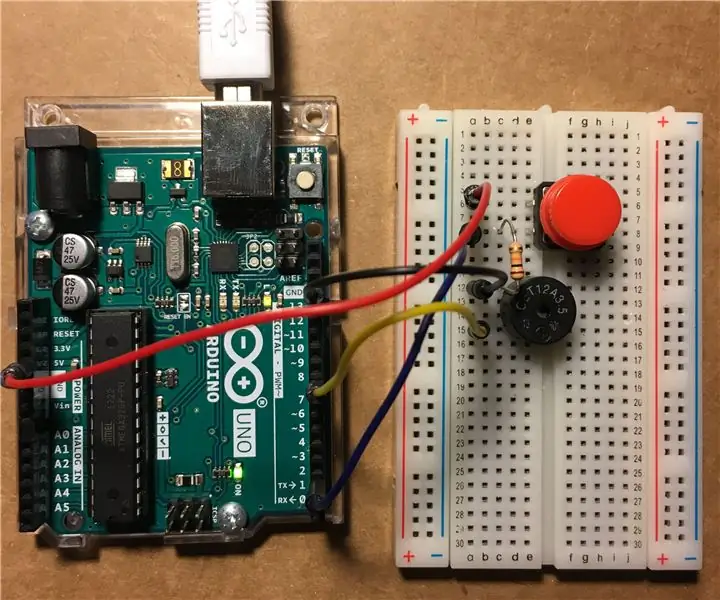
3D robotarm med Bluetooth-styrda stegmotorer: I denna handledning kommer vi att se hur man gör en 3D robotarm, med 28byj-48 stegmotorer, en servomotor och 3D-tryckta delar. Tryckt kretskort, källkod, elektriskt diagram, källkod och massor av information finns på min webbplats
Vifta med handen för att styra OWI robotarm Inga strängar kopplade: 10 steg (med bilder)
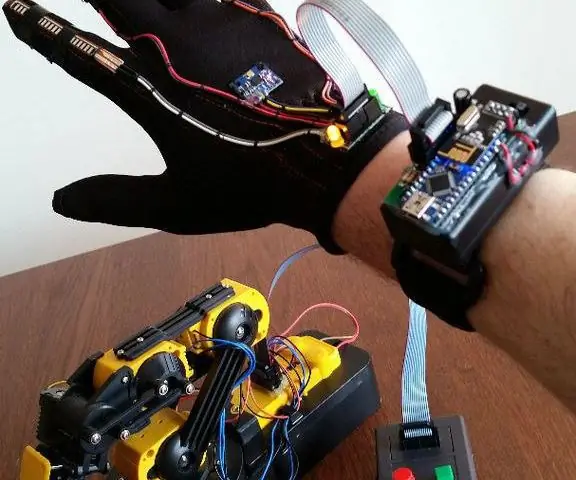
Vifta med handen för att styra OWI Robotic Arm … Inga strängar bifogade: IDÉEN: Det finns minst 4 andra projekt på Instructables.com (från och med den 13 maj 2015) kring att ändra eller styra OWI Robotic Arm. Inte överraskande, eftersom det är ett så bra och billigt robotkit att spela med. Detta projekt liknar i
Arduino kontrollerad robotarm med 6 frihetsgrader: 5 steg (med bilder)
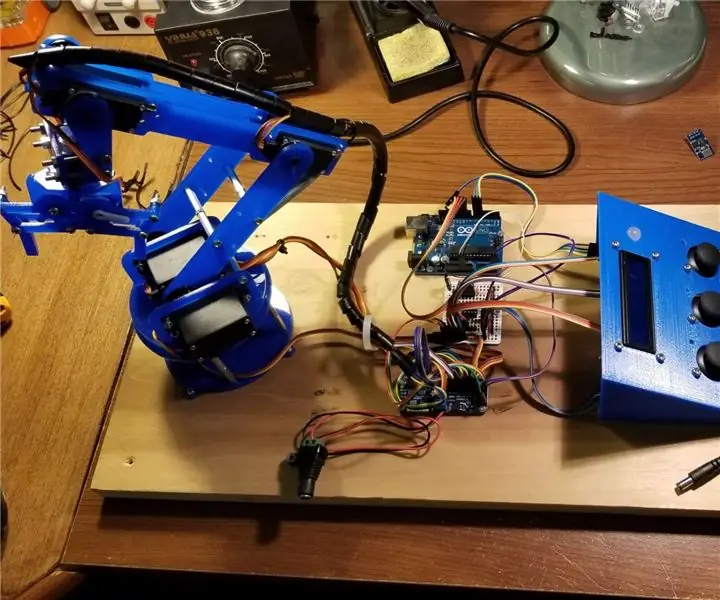
Arduino kontrollerad robotarm med 6 frihetsgrader: Jag är medlem i en robotgrupp och varje år deltar vår grupp i en årlig Mini-Maker Faire. Från och med 2014 bestämde jag mig för att bygga ett nytt projekt för varje års evenemang. På den tiden hade jag ungefär en månad innan evenemanget att sätta ihop något
DigiLevel - en digital nivå med två axlar: 13 steg (med bilder)
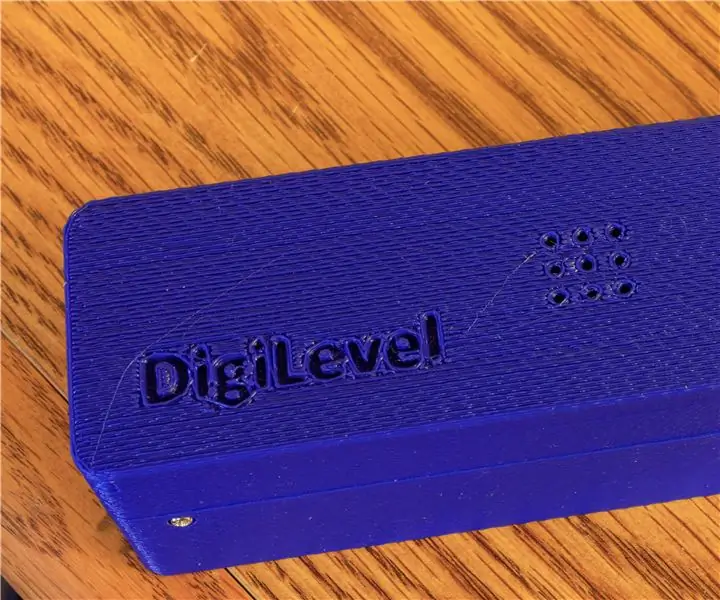
DigiLevel - en digital nivå med två axlar: Inspirationen för denna instruerbara är DIY Digital Water Level som finns här av GreatScottLab. Jag gillade den här designen, men ville ha en större skärm med ett mer grafiskt gränssnitt. Jag ville också ha bättre monteringsalternativ för elektroniken i fodralet