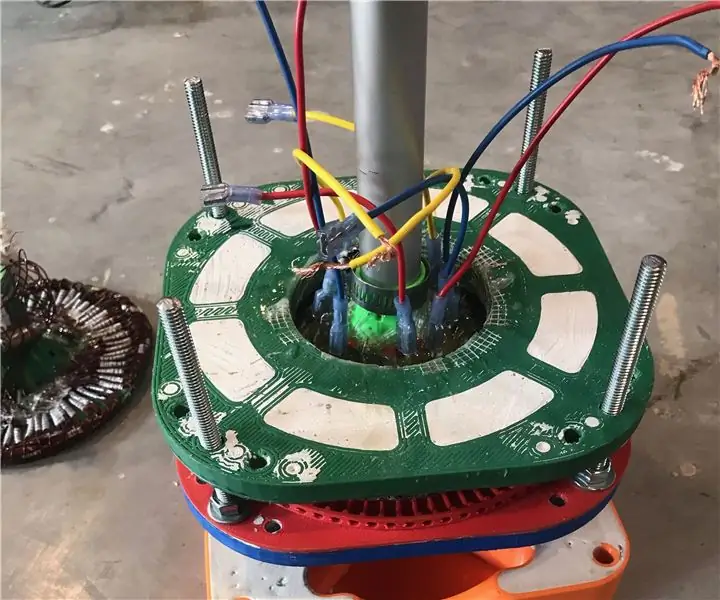
Innehållsförteckning:
2025 Författare: John Day | [email protected]. Senast ändrad: 2025-01-23 15:11
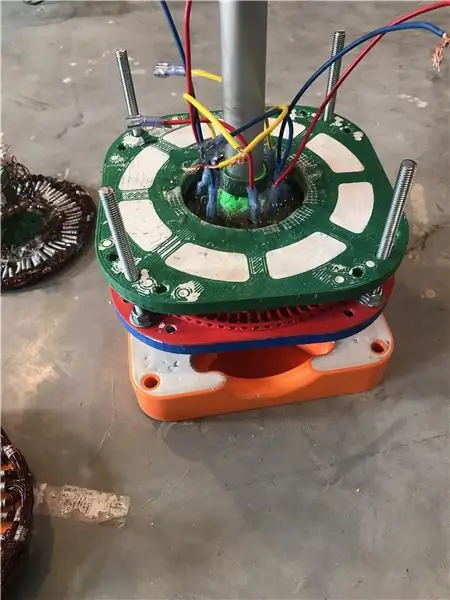
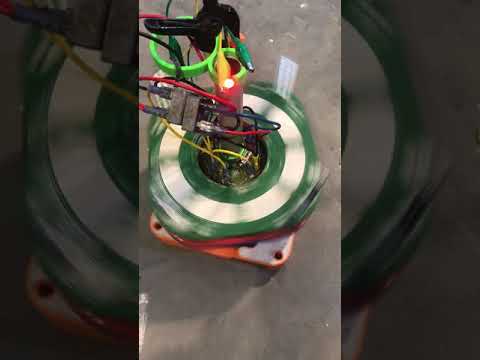
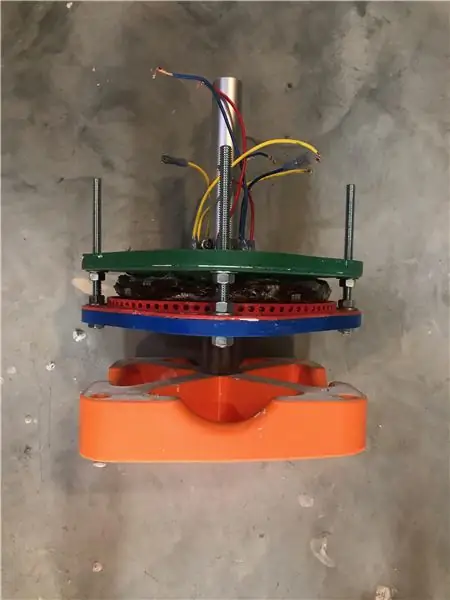
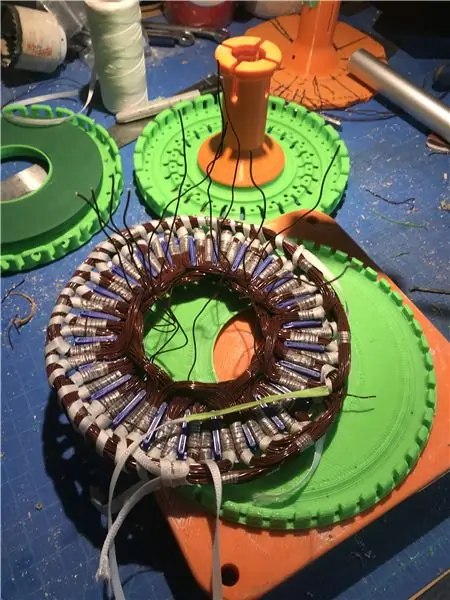
SLUTA!! LÄS DETTA FÖRST !!! Detta är ett register över ett projekt som fortfarande är under utveckling, var god och erbjud support.
Mitt slutliga mål är att denna typ av motor/generator kan bli en parametrerad öppen källkod design. En användare bör kunna ange några parametrar, som vridmoment, hastighet, ström, volt/varv, vanliga magnetstorlekar och kanske ledigt utrymme, och en serie 3D -utskrivbara.stl- och.dxf -klippfiler bör genereras.
Det jag har gjort är att skapa en plattform som kan validera en simulerad design, som sedan kan utvecklas till en mer optimal enhet av gemenskapen.
Dels är detta en anledning till att jag har ställt in detta med en dynamometer. En dynamometer mäter vridmoment och hastighet för att möjliggöra mätning av hk eller axel Watt. I det här fallet har jag byggt generatorn med en genomgående, stationär axel, vilket gör installationen av ett dynamometersystem enklare, och så kan den konfigureras för att drivas som en motor av en RC ESC (hoppas jag) och vridmoment mätt på utgången, samt hastighet, V och förstärkare, så att motoreffektiviteten kan bestämmas.
För mina ändamål kan den drivas av en motor med variabel hastighet (överskott från sladdlös borrmaskin, med nedväxlad växel), och mätning av axelmoment, samt V och ampere ut, vilket möjliggör verklig verkningsgrad och de förväntade turbinbelastningarna att simuleras.
I det här läget hoppas jag kunna använda en RC ESC som kan regenerativ bromsa, och kanske en Arduino för att styra belastningen min VAWT bär för att uppnå MPPT (Multi Power Point Tracking).
MPPT används för såväl sol- som vindturbinkontroll, men det är lite annorlunda för vind. Med vindkraft är en stor fråga att när vindhastigheten fördubblas 10 km/tim till 20 km/tim, ökar energin från vinden med kuben, så med 8 gånger. Om 10W var tillgängligt vid 10 km/tim, så är 80W tillgängligt vid 20 km/tim. Det är fantastiskt att ha mer energi, men generatorernas utgång fördubblas bara som hastigheten fördubblas. Så om du har den perfekta generatorn för en vind på 20 km/h kan belastningen vara så stark att den inte startar vid 10 km/tim.
Vad MPPT gör är att använda en kraftig solid state -omkopplare för att koppla bort och sedan återansluta en generator väldigt snabbt. Det låter dig justera hur mycket belastning en generator bär, och Multi, av MPPT, innebär att du kan ställa in olika belastningar för olika hastigheter.
Detta är mycket användbart, eftersom alla typer av turbiner samlar sin maximala energi när lasten matchas med tillgänglig energi eller vindhastighet.
SÅ
Detta är inte ett recept, även om jag tror att det kan kopieras från det jag har lagt upp, och skulle gärna ge ytterligare information, men jag föreslår att det bästa alternativet vore att föreslå förbättringar för mig innan tävlingarna för kretsar och sensorer slutar, så att jag kan överväga, svara och kanske förbättra detta instruerbart.
Jag kommer att fortsätta att uppdatera, revidera och lägga till information, så om det är intressant nu kanske du vill checka in igen om ett tag, men jag hoppas att jag kan göra en hel del innan Sensors -tävlingen slutar 29/19 juli.
Jag är inte heller ett särskilt socialt djur, men jag gillar en klapp på axeln då och då, och det är en av anledningarna till att jag är här:-) Berätta om du tycker om att se mitt arbete och vill se mer tack:-)
Detta projekt kom för att jag ville ha en kontrollerbar last för att testa mina turbinutformningar, och jag ville att det skulle vara lätt att reproducera, så att andra också kunde använda det. För detta ändamål begränsade jag mig till att designa något som bara kunde byggas med en FDM -skrivare, inga andra verktygsmaskiner behövs. Det verkar inte finnas många kommersiella produkter som fyller behovet av ett högt vridmoment, låg hastighet, icke -kuggande generator, även om det finns några från Kina. I allmänhet är det inte mycket efterfrågan eftersom växelsystem är så billiga och el är så billig.
Vad jag ville var något som producerade runt 12V vid 40-120 rpm och runt 600-750W vid 120-200rpm. Jag ville också att den skulle vara kompatibel med billiga 3 -fas PMA -styrenheter från RC -världen (ESC: s elektroniska hastighetsregulatorer). Ett sista krav var att det skulle vara en utlöpare (hölje eller skal med magneter roterar, medan axel med stator är stillastående), med en axel som passerar hela vägen genom höljet och en stator som kläms fast på axeln.
Detta instruerbara är ett pågående arbete, och jag lägger ut det så att människor kan få en bild av processen, inte så mycket eftersom jag tycker att de borde kopiera den. En viktig sak som jag skulle ändra är att trådstödsplattan jag byggde inte är tillräckligt stark för att ordentligt kanalisera magnetfälten runt ringen, så en stor del av det magnetiska flödet som betalas för dessa magneter är bortkastat på baksidan. När jag gör om designen, vilket jag kommer att göra inom kort, skulle jag troligen göra det som magnetiska stödplattor som cnc -skurna stålplåtar. Stål skulle vara ganska billigt, mycket starkare och förenkla det mesta av detta bygge. Det var intressant att göra FDM/tråd/gips kompositer som jag har illustrerat här, och med järnbelastad PLA hade saker och ting också varit annorlunda. Jag bestämde mig dock för att jag ville ha något som verkligen skulle hålla, så stålplåtar.
Jag har gjort goda framsteg med denna version, som jag ska använda för att testa denna VAWT. Jag är inte riktigt där när det gäller lågspänningsprestanda ännu. Jag tror att min effekt/vridmoment är i rätt bollplatta, jag uppdaterar allt eftersom saker går framåt men vid det här laget har jag en bra chans att vara den kontrollerbara belastningen jag behöver. När den är kortsluten verkar den kunna ge en hel del vridmomentmotstånd, mer än tillräckligt för att testa turbinen. Jag behöver bara skapa en kontrollerad motståndsbank, och jag har en vän som hjälper mig med det.
En sak som jag kort kommer att ta upp är att som många andra har jag haft en 3D-skrivare (FDM-användande PLA) i några år, som jag har haft 20-30 kg njutning av. Jag tycker ofta att det är frustrerande, eftersom delar av valfri storlek/styrka antingen är dyra och mycket långsamma att skriva ut, eller billiga, snabba och tunna.
Jag vet hur många tusentals av dessa 3D -skrivare som finns där ute, som ofta inte gör någonting för att det tar för lång tid eller kostar för mycket att göra användbara delar. Jag har kommit på en intressant lösning för starkare snabbare delar från samma skrivare och PLA.
Jag kallar det en "hällt struktur", där det tryckta föremålet (som består av 1 eller flera tryckta delar, och ibland lager och axlar), är gjorda med hålrum som är avsedda att hällas fulla av ett härdande vätskefyllmedel. Naturligtvis skulle några av de självklara valen för en hällt fyllning vara något liknande epoxi laddad med kortsträngad hackad glasfiber, som kan användas för höghållfasta och lätta vikter. Jag testar lite billigare, mer miljövänliga idéer också. Den andra sidan av denna "hällda struktur" -enhet är att hålrummet eller tomrummet du ska fylla, kan ha element med hög draghållfasthet med liten diameter, förspända på den tryckta "formen/pluggen", vilket gör den resulterande strukturen en komposit i material, och i struktur, del Stressad hud (PLA -manteln), men med en hög komprimerad strängkärna som också innehåller element med hög draghållfasthet. Jag kommer att göra en andra instruerbar med detta, så kommer att prata om det här, bara för att täcka hur det hänför sig till detta bygge.
Steg 1: Materiallista och process
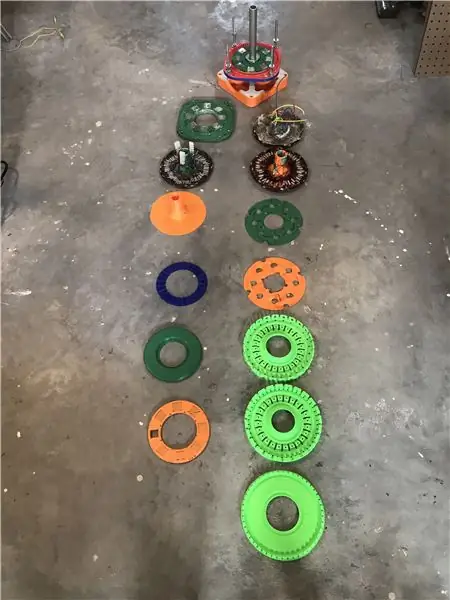
PMA består av 3 sammansättningar, varje enhet innehåller eller använder en mängd olika delar och material.
Uppifrån (lagersidan) till botten (statorsidan), 1. Lagerhållare och topplager
2. Stator
3. Nedre magnetmatris
1. bärhållaren och toppmagneten
För detta använde jag 3D -tryckta delar listade ovan
- 150 mm 8 -polig övre mag och lagerstöd CV5.stl,
- lagersidan inre plattan
- bärsidans yttre platta
- 1 "ID självjusterande lager (som används i vanliga kuddeblock ++ lägg till internetlänk),
- 25 'av 24g galvaniserad ståltråd
- 15 'av 10g galvaniserad ståltråd
- 2 rullar grov stålull
Eventuellt kan den tunga ståltråden och stålullen ersättas med stålplåtar, laser- / vattenstrålesnitt eller en 3D -tryckt magnetisk bakplatta kan vara möjlig (men tung ståltråd är fortfarande en bra idé eftersom den kommer att motstå plastisk deformation över tid). Jag har provat att gjuta en bakplatta med epoxi fylld med järnoxidpulver och lyckats. Att förbättra flödeskopplingen mellan magneter i matrisen i sidled genom att använda en mer effektiv stödplatta bör öka volt ut vid lägre varvtal. Det är också bra att komma ihåg att detta är den viktigaste strukturella komponenten, och bakplattan överför krafterna från magneterna till domkraftsstolparna. De magnetiska krafterna som drar plattorna mot varandra kan vara hundratals kg, och krafterna ökar exponentiellt (Cubed, till den tredje kraften) när plattorna kommer nära varandra. Detta kan vara mycket farligt, och försiktighet måste iakttas med verktyg och andra föremål som kan lockas till den monterade plattan eller den är tillbaka!
Jag använde cirka 300 fot 24g belagd magnettråd i lindningarna som jag kommer att täcka i detalj senare.
Steg 2: Tillverkning av magnetplattorna
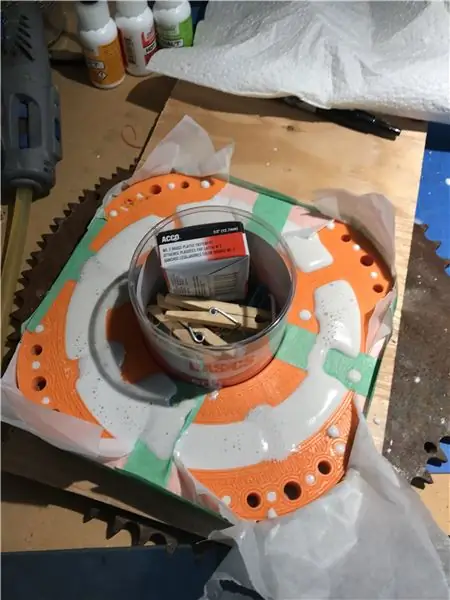
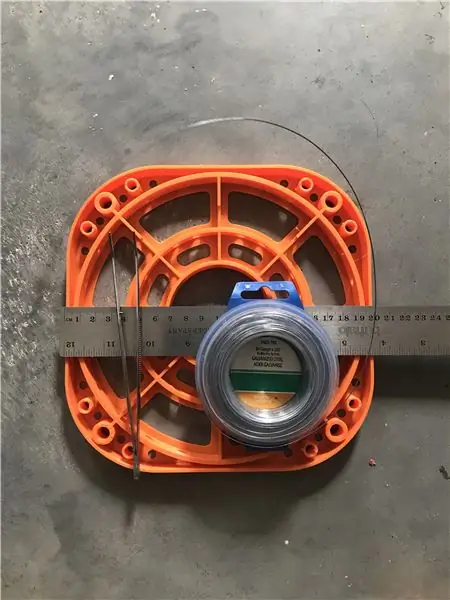
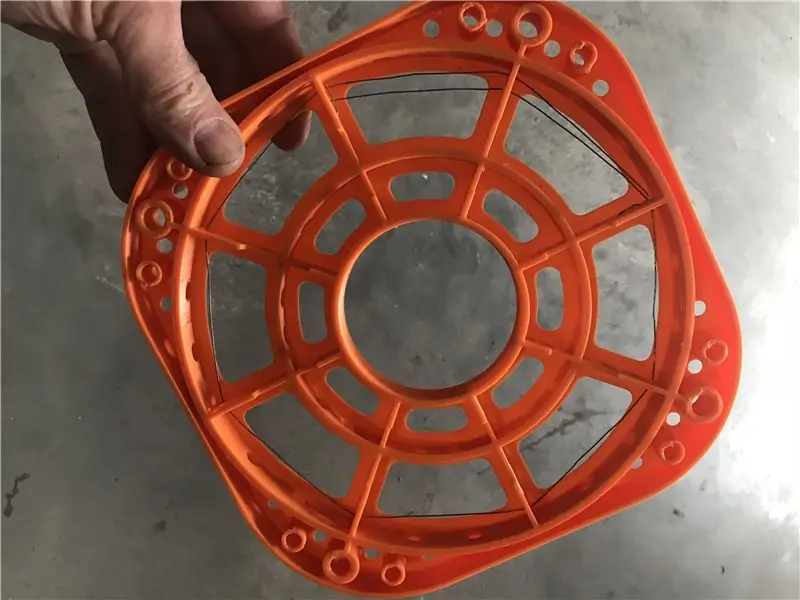
I denna axiella flödesgenerator, för att minimera kuggning och maximera produktionen, använder jag två magnetuppsättningar, en på varje sida av statorspolarna. Detta innebär att ingen magnetkärna behövs för att dra magnetfältet genom kopparlindningarna, som de flesta motor/alt geometrier gör. Det finns några axiella flödesdesigner som använder pariserkärnor, och jag kan prova några experiment på det sättet i framtiden. Jag skulle vilja prova något 3D -utskrivbart järnladdat material.
I det här fallet har jag valt en 8 -polig magnetuppsättning i ungefär en 150 mm cirkel, med hjälp av 1 "x1" x0.25 "sällsynta jordartsmagneter. Denna storlek var för att säkerställa att alla delar skulle passa på en 210 mm x 210 mm tryckbädd. I allmänhet dimensionerade jag den här generatorn först genom att förstå att ju större diameter, desto bättre när det gäller volt per varv, så den blev så stor som bekvämt skulle passa min trycksäng. FYI, det finns mer än en anledning större är bättre: mer plats för magneter, ju längre magneterna är från mitten, desto snabbare reser de, och det finns också mer utrymme för koppar! Alla dessa saker kan bli snabba! Men en slutsats som jag kommit fram till är att i detta storleksintervall är en konventionell flussystem kan vara ett bättre hembygge. Små rotorer har inte mycket utrymme och saker kan bli ganska snäva, särskilt om du gör en genomgående axel som jag har gjort i denna design. Även om din magnet (radiell längd) är liten i förhållande till din rotordiameter, som i den här, (ungefär 6 "diameter till 1" magnet), sedan ng blir lite konstigt med den inre ändlindningen som bara är ungefär 1/2 av den yttre längden.
Tillbaka till instruktionen! Det sätt jag har monterat magnetplattorna på denna generator är att först limma magnetplattan (grön) på den röda flänsen/stödplattan. Jag placerade sedan magnetplattan på några tunna lager plywood (cirka 0,75 tum tjocka) och placerade båda på en tung stålplåt för att låta magneterna klämma fast enheten. Sedan lindade jag ståltråd på baksidan av magnetplattorna. Detta gick inte riktigt som jag hade hoppats. Det starka magnetfältet drog tråden mot mitten av magneterna, och jag lyckades inte böja varje rad, av tråd för att passa perfekt till nästa plats, utan att skada den första omslaget. Jag hade hoppats att jag bara kunde spola in tråden och magnetflödet skulle låsa den. Därefter försökte jag klippa trådringar, och det här var bättre, men fortfarande långt ifrån vad jag hade hoppades när det gäller att få en fin konsekvent stödplatta från tråd. Mer komplexa sätt att få detta gjort är möjliga och kan vara värda framtida experiment. Jag försökte också använda stålull, komprimerad i magnetfältet, som en stödplatta eller fluss Detta verkade fungera, men den verkliga järntätheten verkade inte vara särskilt hög, så jag di testade inte dess effektivitet, delvis för att jag trodde att trådstrukturen var viktig för de mekaniska belastningarna på magnetplattorna. Stålullen kan också vara värd framtida undersökningar, men vattenstråleslipade stålplåtar är troligtvis nästa alternativ som jag kommer att försöka.
Därefter tog jag den orange 3D -tryckta delen och vävde tråd genom och runt den, längs det som tycktes vara riktningarna för högsta belastning, bult till bult och bult för att centrera några gånger i varje hörn. Jag lindade den också runt bulthålen där hela trådstången passerar som domstolpar för att hålla och justera avståndet mellan plattorna.
Efter att ha varit nöjd med att magnetplattan och flänsen var tillräckligt bra och den orange stödplattan var tillfredsställande gängad med förstärkningstråd, förenade jag de två med lim. Var försiktig eftersom denna limfog måste vara vattentät eller stänga. Jag hade läckor de två första gångerna, och det är en röra, slösar bort mycket gips och är mer stress än du behöver. Jag skulle rekommendera att hålla lite blå klibb eller annat tuggummi som icke permanent lim runt för att lappa läckage snabbt. När delarna är sammanfogade fyller du med förstärkningsmaterialet efter eget val. Jag använde en hård gips, modifierad med PVA -lim. Gipset ska uppgå till 10 000 psi komprimerat, men inte mycket i spänning (alltså tråden). Jag skulle vilja prova epoxi med hackat glas och cabosil, eller betong och tillsatser.
En praktisk sak med gipset är att när det väl har börjat har du ganska mycket tid där det är svårt, men ömtåligt och läckor eller fläckar kan lätt skrapas eller slås av.
I denna design finns det två magnetplattor. Den ena har ett lager, en standard 1 självjusterande kuddeblock. Jag tryckte tidigt in min i magnetuppsättningen. För applikationen jag har konstruerat den för kommer ett andra lager att placeras i turbinen ovanför generatorn, så jag använde bara det ena självjusterande lagret. Detta var lite smärtsamt i slutändan. Dessa delar kunde också monteras med varje magnetplatta som har ett lager, om utgångstrådarna från statorn leddes internt genom den monterade axeln. Detta skulle låta kontra roterande drivmedel monteras på en gemensam, icke -roterande axel/rör.
Steg 3: Skapa Stator

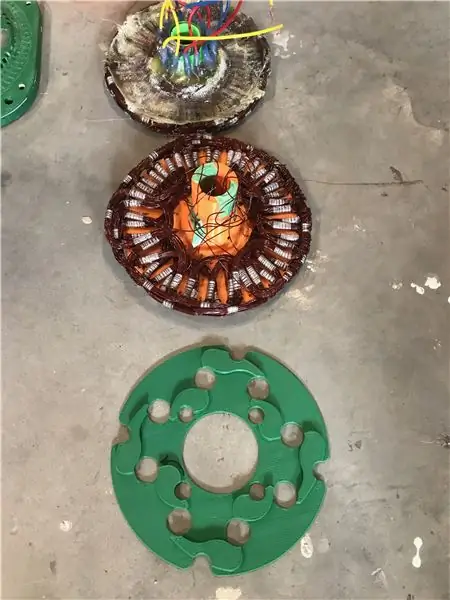
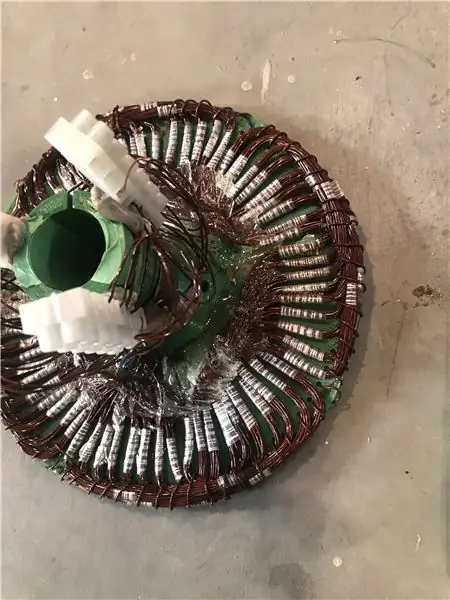
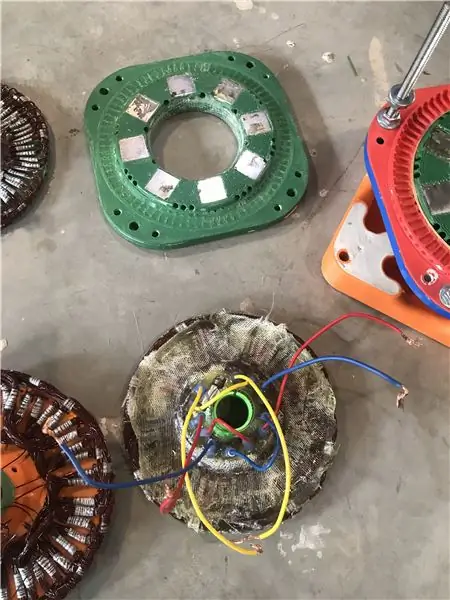
I linje med mitt tema att försöka förklara vad jag har gjort och varför det verkade som en bra idé då, kommer statorn att kräva lite mer utrymme.
I en PMA är lindningarna i allmänhet stationära medan de magnetiska enheterna roterar. Detta är inte alltid fallet, men nästan alltid. I ett axiellt flödesaggregat, med förståelsen av den grundläggande "högerregeln", är det underförstått att varje ledare som stöter på ett roterande magnetfält kommer att få ström och spänning mellan trådens ändar, med mängden användbar ström proportionell. till fältets riktning. Om fältet rör sig parallellt med tråden (t.ex. i en cirkel runt rotationsaxeln) kommer ingen användbar ström att genereras, men betydande virvelströmmar genereras som motstår magneternas rörelse. Om tråden går vinkelrätt kommer den högsta spänningen och strömutgången att nås.
En annan generalisering är att utrymmet i statorn, genom vilket det magnetiska flödet passerar medan det är i rotation, för maximal effekteffekt, ska fyllas med så mycket koppar, allt radiellt lagt, som möjligt. Detta är ett problem för axiella flusssystem med liten diameter, eftersom i detta fall är det tillgängliga området för koppar nära axeln en bråkdel av området vid ytterkanten. Det är möjligt att få 100% koppar i det mest inre området som magnetfältet stöter på, men inom denna geometri ger det dig kanske bara 50% vid ytterkanten. Detta är en av de starkaste anledningarna till att hålla sig borta från axialflödesdesigner som är för små.
Som jag har sagt tidigare handlar detta instruerbara inte om hur jag skulle göra det igen, det är mer att peka i några riktningar som verkar lovande och visa upp några av de gropar som kan nås på denna väg.
Vid utformningen av statorn ville jag göra den så flexibel som möjligt när det gäller volymeffekt per varv / min, och jag ville att den skulle vara 3 -fas. För maximal effektivitet, genom att minimera virvelströmmar som genereras, bör varje "ben" (varje sida av en spole betraktas som ett "ben") bara möta en magnet åt gången. Om magneterna är nära varandra, eller vidrör som är fallet i många högeffekt -rc -motorer, kommer under tiden "benet" passerar genom magnetflödesomvändningen att utvecklas betydande virvelströmmar. I motorapplikationer spelar det inte så stor roll, eftersom spolen drivs av regulatorn när den är på rätt plats.
Jag dimensionerade magnetmatrisen med dessa koncept i åtanke. De åtta magneterna i matrisen är var och en 1 "tvärs och utrymmet mellan dem är 1/2". Det betyder att ett magnetiskt segment är 1,5 "långt och har plats för 3 x 1/2" "ben". Varje "ben" är en fas, så när som helst ser ett ben neutralt flöde, medan de andra två ser accending flux och minskar flux. Perfekt 3 -fas utgång, men genom att ge neutralpunkten så mycket utrymme (för att minimera virvelströmmar) och med fyrkantiga (eller pajformade) magneter når flödet nästan tidigt, förblir högt och faller sedan snabbt till noll. Jag tror att denna typ av utsignal kallas trapetsformad och kan vara svår för vissa kontroller som jag förstår. 1 "runda magneter i samma apparat skulle ge mer av en sann sinusvåg.
I allmänhet har dessa hembyggda generatorer byggts med "spolar", munkformade trådbuntar, där varje sida av munken är ett "ben" och antalet spolar kan fästas ihop, i serie eller parallellt. Munkarna är arrangerade i en cirkel, med deras centrum i linje med mitten av magnetbanan. Detta fungerar, men det finns några problem. En fråga är att eftersom ledarna inte är radiella, passerar en stor del av ledaren inte vid 90 grader till magnetfältet, så genereras virvelströmmar, som uppträder som värme i spolen och motstånd mot rotation i magnetuppsättningen. En annan fråga är att eftersom ledarna inte är radiella, packar de inte ihop lika fint. Utgången är direkt proportionell mot mängden tråd du kan passa i detta utrymme, så utmatningen reduceras med icke -radiella "ben". Även om det skulle vara möjligt och ibland görs i kommersiella utföranden, kräver det att du lindar en spole med radiella "ben, sammanfogade upptill och nedtill, 2x så mycket ändlindning som en serpentinlindning där toppen av ett ben är förbunden med toppen av nästa lämpliga ben, och sedan botten av det benet är förenat med nästa lämpliga ben, och på och på.
Den andra stora faktorn i Axial fluxgeneratorer av denna typ (roterande magneter över och under stator) är gapet mellan plattorna. Detta är ett kubslag, eftersom du minskar avståndet mellan plattorna med 1/2, magnetflödestätheten ökar med 8x. Ju tunnare du kan göra din stator, desto bättre!
Med detta i åtanke gjorde jag en 4 -flikig lindningsjigg, satte upp ett system för att mäta ut cirka 50 fot trådtrådar och lindade jiggen 6 gånger och skapade trådbuntar med en diameter på cirka 6 mm. Dessa passar jag på den blå avståndsringen och knyter dem genom hålen så att trådändarna kom ut på baksidan. Detta var inte lätt. Det hjälpte lite genom att försiktigt tejpa ihop buntarna så att de inte var lösa, och genom att ta mig tid och använda ett smidigt träformningsverktyg för att skjuta trådarna på plats. När de alla var bundna på plats placerades den blå avståndsringen i den största av de ljusgröna formkärlen, och med hjälp av det mörkgröna munformningsverktyget, på andra sidan av det ljusgröna badkaret, pressades det försiktigt platt med en bänkskruv. Denna formningskärl har ett spår för snoddtrådarna att sitta i. Detta tar tid och tålamod när du försiktigt roterar cirka 1/5 varv, trycker, roterar och fortsätter. Detta formar skivan platt och tunn, samtidigt som ändlindningarna kan staplas. Du kanske märker att min 4 -flikiga lindning har raka "ben" men de inre och yttre anslutningarna är inte runda. Detta var tänkt att göra det lättare för dem att stapla. Det gick inte så bra. Om jag skulle göra det igen skulle jag få insidan och utsidan av lindningarna att följa cirkulära banor.
Efter att ha fått det platt och tunt och kanterna packade ner lindade jag ett platt band runt kanten för att komprimera det, och ett annat upp, ner och runt varje ben och sedan till det bredvid det också. När detta är gjort kan du ta bort sladdtrådarna och byta till det mindre pressbadet, gå tillbaka till skruven och tryck på den så tunn och platt som möjligt. När den är platt tar du bort den från presskaret. Istället för den komplexa processen med att noggrant vaxa och belägga formar som denna med släppföreningar använder jag vanligtvis bara ett par lager stretchfolie (från köket). Lägg ett par lager i formens botten och lägg glasfiber på stretchfolien. Lägg sedan till statormonteringsröret, som passar till toppen av det ljusgröna formkärlet, men har lagret av stretchfolie och glasfiber mellan. Lägg sedan tillbaka statorlindningen på plats för att trycka ner både stretchfolien och glasfiber och låsa stators monteringsrör på plats. Återgå sedan till skruven och tryck platt igen. När det väl passar in i badkaret, med stretchfolien och glasfiber inklämt, läggs glasfiberduk till (med ett hål i mitten för stators monteringsrör).
Nu är det klart att hälla bindningsmaterialet, epoxi eller polyesterharts används ofta. Innan detta är gjort är noggrann förberedelse viktig eftersom när du väl har startat denna process kan du inte riktigt sluta. Jag använde en 3D -tryckt basplatta som jag tidigare hade gjort, med ett 1 "hål i mitten och en platt platta runt den. Jag använde en 16" bit av 1 "aluminiumrör, som statormonteringsröret skulle passa över och vara hölls vinkelrätt mot den platta plattan. Det gröna formkärlet, statorlindningen och statormonteringsröret gled ner för att sitta på den platta plattan. Innan jag blandade epoxi redo jag först 4 bitar av krympfolie och placerade försiktigt en femte bit på mörkgrön formande munk, så den skulle ha minsta rynkor i ansiktet mot statorlindningen. Efter att ha blandat epoxyn och hällt den på glasfiberduken, lade jag försiktigt ner stretchfolien runt 1 "-röret och placerade greenen bildande ring ovanpå den. Jag hade också förberett ett par gamla bromsrotorer, vilket gav lite vikt, och satt fint på den gröna formande munken. Efter detta lade jag en omvänd kruka ovanpå bromsrotorerna och ovanpå potten staplade jag cirka 100 kg grejer. Jag lämnade detta i 12 timmar, och det kom ut ca 4-6 mm tjockt.
Steg 4: Testning och sensorer
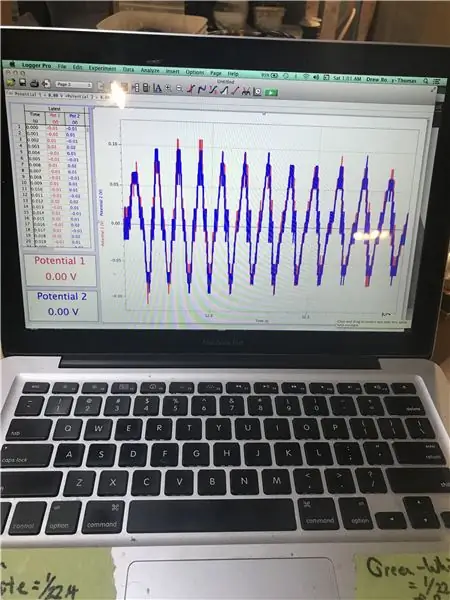
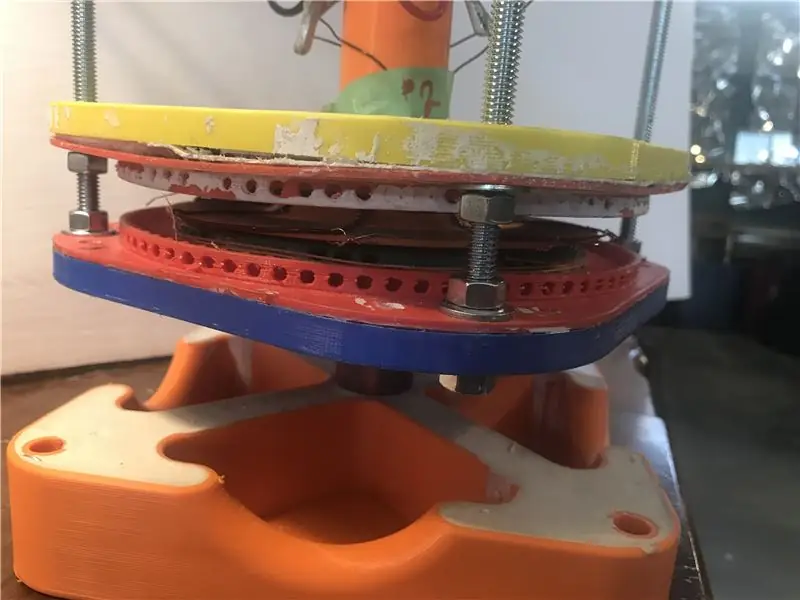
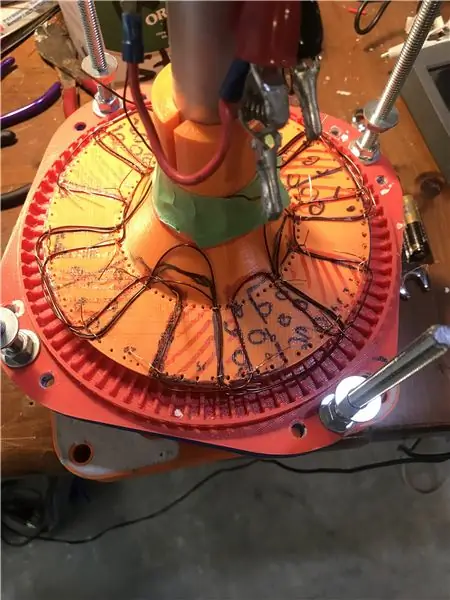
Det finns ett antal mätbara in- och utgångar från generatorn, och det är inte lätt att mäta dem alla samtidigt. Jag är mycket lyckligt lottad som har några verktyg från Vernier som gör det här mycket enklare. Vernier tillverkar utbildningsnivåprodukter, inte certifierade för industriellt bruk, men mycket hjälpsamma för experimenter som jag själv. Jag använder en Vernier -datalogger med en mängd olika plug and play -sensorer. På detta projekt använder jag hallbaserade ström- och spänningssonder, för att mäta generatorns utgång, en optisk sensor för att ge generatorns hastighet och en lastcell för att mäta vridmomentinmatning. Alla dessa instrument samplas cirka 1000 gånger per sekund och spelas in på min bärbara dator med Vernier -loggen som en AD -genomströmningsenhet. På min bärbara dator kan den associerade programvaran köra realtidsberäkningar baserade på ingångarna, som kombinerar vridmoment- och hastighetsdata för att ge realtid ingångsaxeleffekt i watt och utdata i realtid i elektriska watt. Jag är inte klar med denna testning, och input från någon som har en bättre förståelse skulle vara till hjälp.
En fråga som jag har är att den här generatorn verkligen är ett sidoprojekt, så jag vill inte lägga alltför mycket mer tid på det. Som det är tror jag att jag kan använda det för en kontrollerbar belastning för min VAWT -forskning, men så småningom skulle jag vilja arbeta med människor för att förfina det, så att det är en effektiv matchning för min turbin.
När jag började med VAWT -forskning för ungefär 15 år sedan insåg jag att testning av VAWT: s och andra drivkraftverk är mer komplex än de flesta inser.
En primär fråga är att energin som representeras i en rörlig vätska är exponentiell för dess rörelsehastighet. Detta innebär att när du fördubblar hastigheten för ett flöde, ökar energin i flödet 8x (det är kubat). Detta är ett problem, eftersom generatorer är mer linjära och i allmänhet får du ungefär 2x watt om du fördubblar varvtalet för en generator.
Denna grundläggande missmatchning mellan turbinen (energisamlingsanordning) och generatorn (axeleffekt till användbar elektrisk kraft) gör det svårt att välja en generator för ett vindkraftverk. Om du väljer en generatormatch för ditt vindkraftverk som kommer att generera mest tillgänglig effekt från vindar på 20 km/tim kommer det sannolikt inte ens att börja vända förrän 20-25 km/tim eftersom belastningen på turbinen från generatorn blir för hög. Med den generatormatchen, när vinden är över 20 km, kommer inte bara turbinen att fånga upp en bråkdel av den energi som finns i vinden med högre hastighet, turbinen kan överhastas och skadas eftersom lasten från generatorn inte är hög tillräckligt.
Under det senaste decenniet har en lösning blivit mer ekonomisk på grund av prisfallet på kontrollelektronik. I stället för att försöka matcha ett hastighetsintervall beräknar designern den maximala hastighet som enheten är avsedd att arbeta med och väljer en generator baserat på mängden energi och idealhastighet för turbinen vid den hastigheten, eller lite över. Denna generator om den är ansluten till dess belastning skulle normalt ge för mycket vridmoment vid lågt varvtalsintervall, och den överbelastade turbinen kommer inte att fånga upp all energi den kan ha om den var korrekt laddad. För att skapa rätt belastning läggs till en styrenhet som tillfälligt kopplar bort generatorn från den elektriska lasten, vilket gör att turbinen kan snabba upp till rätt hastighet, och generatorn och lasten återansluts. Detta kallas MPPT (Multi Power Point Tracking). Regulatorn är programmerad så att när turbinhastigheten ändras (eller generatorns spänning stiger), är generatorn ansluten eller frånkopplad, tusen gånger per sekund eller så, för att matcha den belastning som programmerats för den hastigheten eller spänningen.
Rekommenderad:
Persienner med ESP8266, Google Home och Openhab -integration och webbkontroll: 5 steg (med bilder)
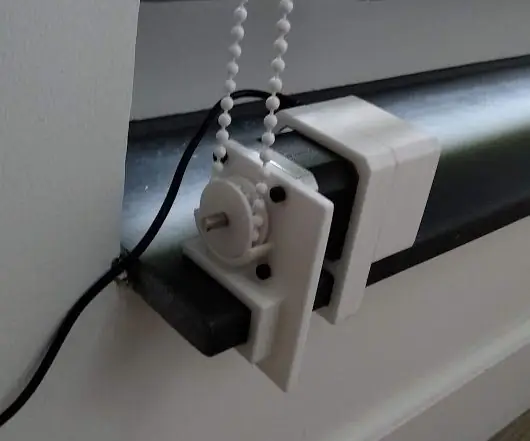
Kontroll av persienner med ESP8266, Google Home och Openhab -integration och webbkontroll: I den här instruktionsboken visar jag dig hur jag lade automatisering till mina persienner. Jag ville kunna lägga till och ta bort automatiseringen, så all installation är klämd på. Huvuddelarna är: Stegmotor Stegdrivrutinstyrd vid ESP-01 Växel och montering
Övervaka och registrera temperatur med Bluetooth LE och RaspberryPi: 9 steg (med bilder)
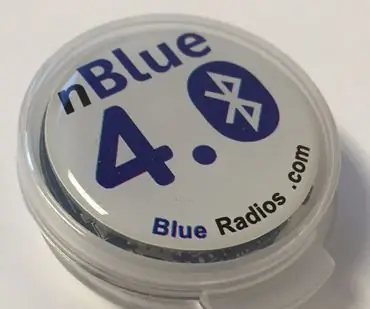
Övervaka och registrera temperatur med Bluetooth LE och RaspberryPi: Den här instruerbara handlingen handlar om hur man sätter ihop ett temperaturövervakningssystem med flera noder med Bluetooth LE-sensorbugg från Blue Radios (BLEHome) och RaspberryPi 3B Tack vare utvecklingen av standarden Bluetooth LE finns det nu tillgängligt
Gör en Air Raid Siren med motstånd och kondensatorer och transistorer: 6 steg (med bilder)
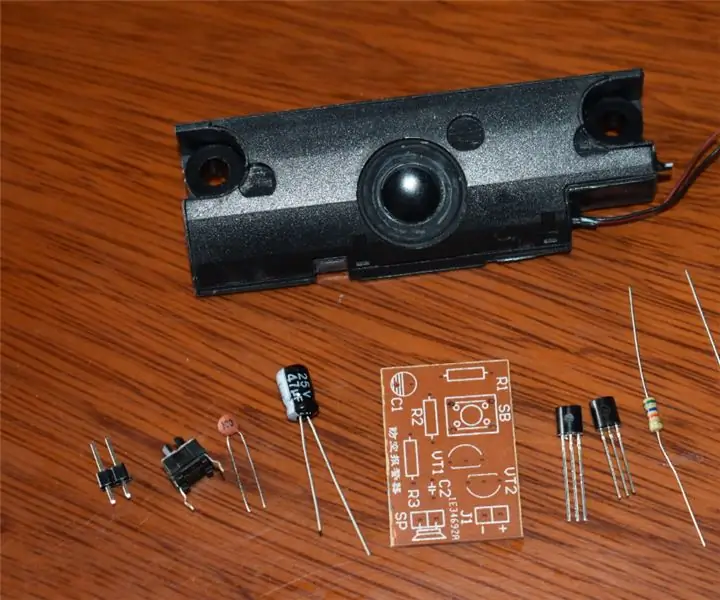
Gör en Air Raid Siren med motstånd och kondensatorer och transistorer: Detta prisvärda Air Raid Siren DIY-projekt är lämpligt för att undersöka självoscillationskrets som består av bara motstånd och kondensatorer och transistorer som kan berika din kunskap. Och den är lämplig för National Defense Education for Kids, i
8 Reläkontroll med NodeMCU och IR -mottagare med WiFi och IR -fjärrkontroll och Android -app: 5 steg (med bilder)
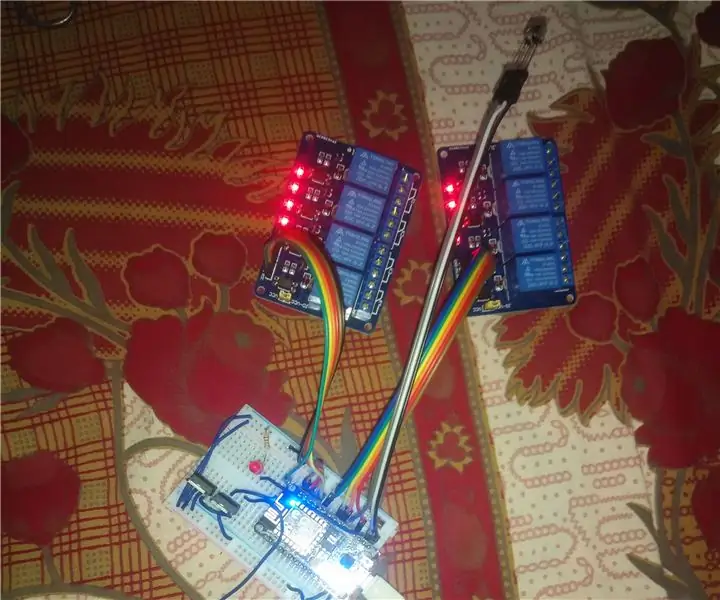
8 Reläkontroll med NodeMCU och IR -mottagare med WiFi och IR -fjärrkontroll och Android -app: Styrning av 8 reläväxlar med nodemcu och IR -mottagare via wifi och IR -fjärrkontroll och Android -app. Fjärrkontrollen fungerar oberoende av wifi -anslutning. HÄR ÄR EN UPPDATERAD VERSIONKLICK HÄR
Temperatur och fuktighet Display och datainsamling med Arduino och bearbetning: 13 steg (med bilder)
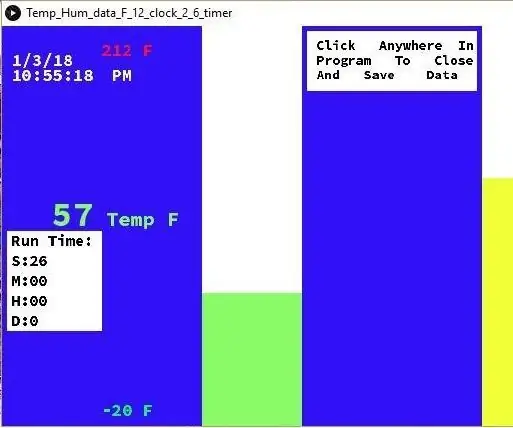
Temperatur- och luftfuktighetsvisning och datainsamling med Arduino och bearbetning: Intro: Detta är ett projekt som använder ett Arduino -kort, en sensor (DHT11), en Windows -dator och ett bearbetningsprogram (ett gratis nedladdningsbart) för att visa temperatur, luftfuktighetsdata i digital och stapeldiagramform, visa tid och datum och kör en räkningstid